Kyocera Group Environmental Safety Policy
The Kyocera Group is committed to creating a safe and secure work environment for our employees through the Kyocera Group Environmental Safety Policy, based on our Management Rationale.
The number of occupational accidents peaked in FY2010 and has been on a downward trend since then, but is expected to increase after FY2020.
Work-related accidents generally result from deficiencies in awareness of safety procedures (training) among inexperienced employees and insufficient risk awareness for specific tasks.
In response, a system for implementing risk assessments has been created; efforts have been made to improve risk identification and countermeasures further; a revamping of the training system for inexperienced employees is under consideration; and, a new type of hazard awareness training has been introduced.
In the medium to long term, we aim to foster operational excellence through safety-focused workplaces. Employees can educate each other through safety management activities in which all employees participate.
Kyocera Group Environmental Safety Policy
Based on Kyocera's founding company motto, "Respect the Devine and Love People," we established our management rationale "To provide opportunities for the material and intellectual growth of all our employees, and through our joint efforts, contribute to the advancement of society and humankind." Therefore, in addition to complying with laws and regulations on environmental safety, requirements agreed to by our company, and our own internal standards, we will continue to work to solve issues critical to society through communication with various stakeholders, participation in and support for social contribution activities, and by leveraging our technology and intellectual know-how.
Ensuring the safety and health of employees
- To create a safe and secure workplace for all employees, we will create a corporate culture in which everyone involved in our business activities is fully engaged.
- Kyocera will conduct risk assessments and reduce occupational health and safety risks by eliminating sources of danger to prevent workplace accidents and disasters.
- Kyocera strives to build a work environment where employees feel healthy, enjoy job satisfaction, and can reach their maximum potential by promoting mental and physical health.
Contribution to a sustainable society
- Kyocera will research, develop, produce, and expand products that contribute to the improvement of the global environment and products that reduce environmental impact throughout their life cycles.
- Kyocera will promote greenhouse gas emission control in our entire value chain to contribute to realizing a carbon-free society.
- Kyocera will contribute to realizing a recycling-oriented society by using resources more efficiently.
- Kyocera will strive to prevent environmental pollution by properly managing chemical substances in all processes.
- Kyocera will advance biodiversity conservation by minimizing the negative impact of our business activities on the natural environment and by protecting and nurturing the natural environment.
Operation of an environmental and safety management system
- During our business activities, through the operation of our management system, the Kyocera Group will proactively promote comprehensive measures for environmental protection and work safety, based on the management rationale, and continuously improve environmental and safety performance.
April 1, 2023
Kyocera Corporation
Hideo Tanimoto, President
Target
The Kyocera Group has established Kyocera Group Environmental Safety Targets, which outline the reduction of Industrial Injuries and fire-related accidents.
Work-related Accident Rate Within Kyocera Group (Japan)
Targets for FY2024 | Work-related accident rate (including Lost-time and without Lost-time accident) is 0.79. The target for the number of fire incident is 0. |
---|---|
Achievements in FY2024 | Achievements in FY2024 Work-related accident rate (including Lost-time and without Lost-time accident) was 0.99. The number of 6 fire incidents. |
Targets for FY2025 | Work-related accident rate (including Lost-time and without Lost-time accident ) is 0.66. The target for the number of fire incident is 0. |
---|
Occupational Safety Promotion System
The Kyocera Group has established a safety management system based on ISO45001 Occupational Health and Safety Management guidelines to promote occupational safety and health.
Environmental and Safety Management System
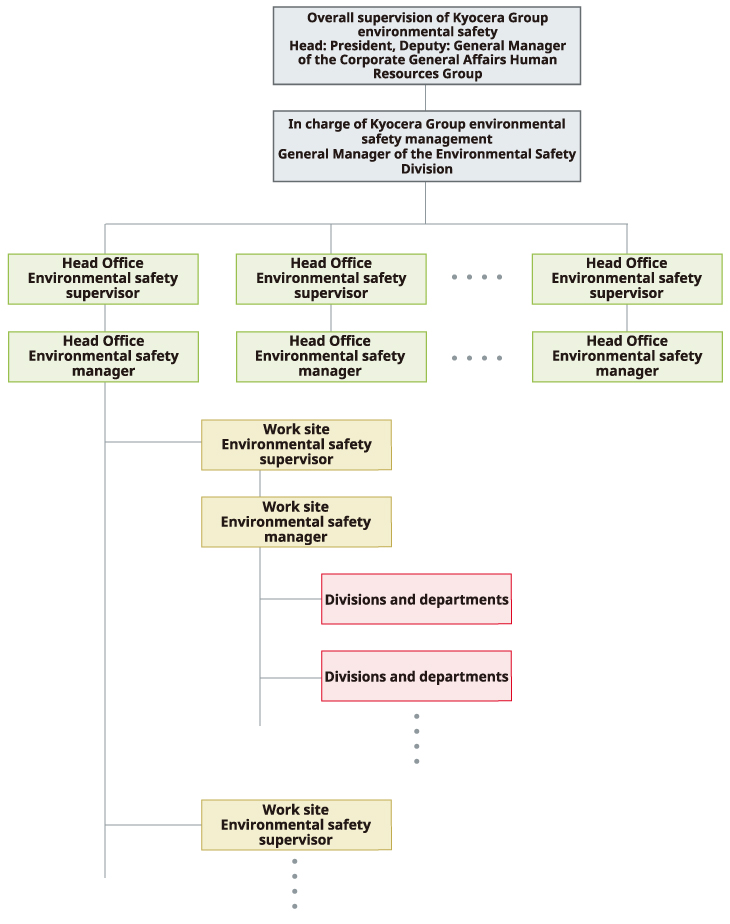
【Integrated Certification】
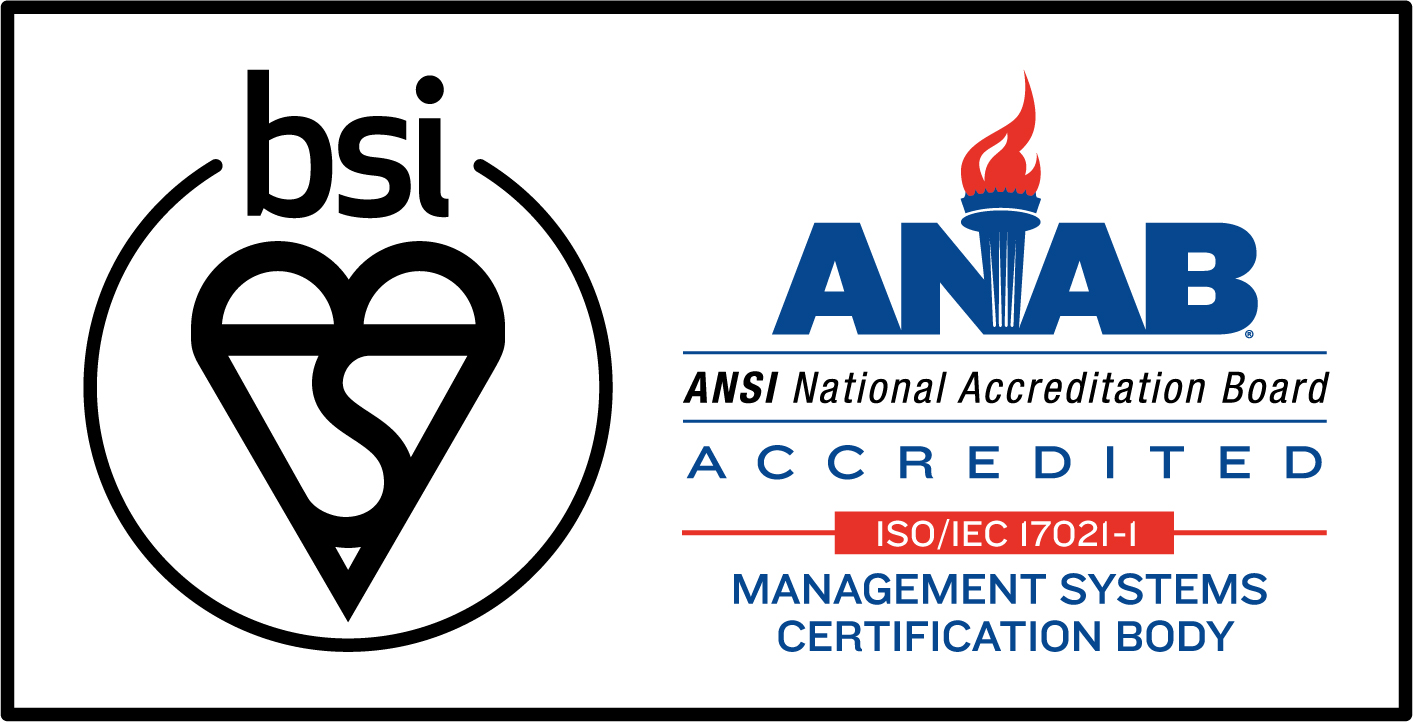
【Individual Certification】
Review of FY2024
Changes Accident Rates (Japan)
The lost-time accident rate of the Kyocera Group (in Japan) in FY2024 was 0.49, lower than the average of all manufacturing industries, as well as the electric machinery and appliance manufacturing industries.
In order to strengthen countermeasures, we analyzed industrial injuries and took measures focusing on work-related accidents (including Lost-time and without Lost-time accidents). As a result, the frequency rate was 0.99 (target: 0.79). There were six fires incidents (target: 0). We investigate the causes of accidents occurring at our worldwide locations and implement safety measures to remove any potential hazards.
Going forward, we will continue to reduce the number of industrial injuries and create a safe and secure working environment for all our employees.
Lost time accident rate
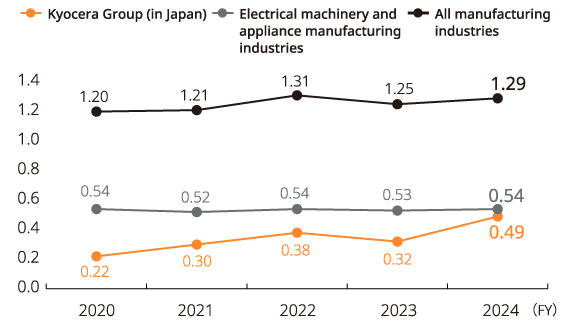
The lost time accident rates of all manufacturing industries and electrical machinery and appliance manufacturing industries are based on data from the Ministry of Health, Labour and Welfare.
Lost time accident rate: Number of afflicted persons / 1 million hours (The number of days of missed work is as per the standards of the Ministry of Health, Labour and Welfare.)
The Ministry of Health, Labour and Welfare figures utilize fiscal year data. (Lost time of one day or more)
Kyocera Corporation and Kyocera Group (in Japan) lost time accident rates utilize fiscal year data. (Lost time of one day or more)
Temporary and part-time employees are excluded
Occupational Disease Rate Within Kyocera Group (Japan)
FY2020 | FY2021 | FY2022 | FY2023 | FY2024 | |
---|---|---|---|---|---|
Occupational disease rate | 0.07 | 0.21 | 0.22 | 0.22 | 0.26 |
The occupational disease has been calculated based on all instances covered by the Appended Table 1-2 of the Ordinance for Enforcement of the Labor Standards Act (including diseases due to physical factors, diseases caused by the nature of the work, injuries caused by chemical substances, and others.)
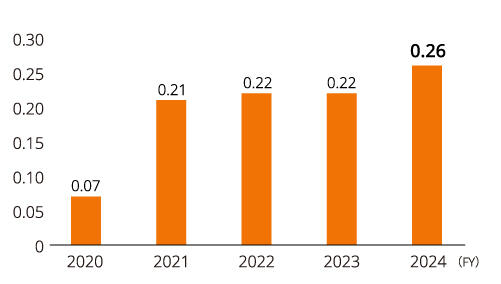
Examples of Major Initiatives
Risk assessment and special patrols
In order to prevent accidents, in Japan, we appoint risk assessment trainers and risk assessors at each business site and continue to develop risk assessment measures. Risk assessment trainers and risk assessors receive practical training and lectures regarding the necessary base knowledge and skills. They then perform risk assessments to gain an understanding of hazards through the appropriate identification and evaluation of risks before implementing countermeasures. This serves to prevent accidents before they occur.
In addition to the previous year's efforts, special patrols were conducted within the group to identify major risks and evaluate the effectiveness of control measures, and to thoroughly address and improve activities to address major risks.
We will continue to make improvements by establishing more effective risk identification methods and improving the capabilities of our risk assessment trainers and risk assessors to prevent accidents.
Risk Assessment Overview
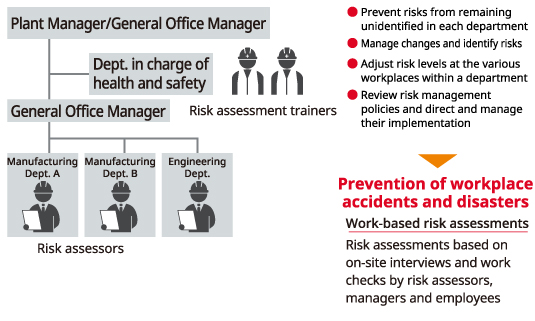
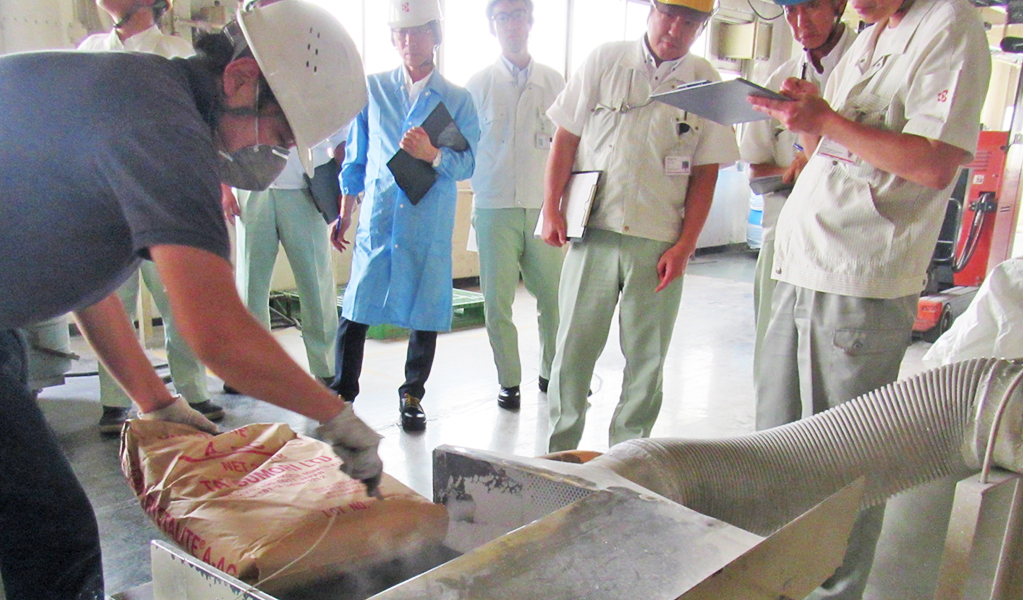
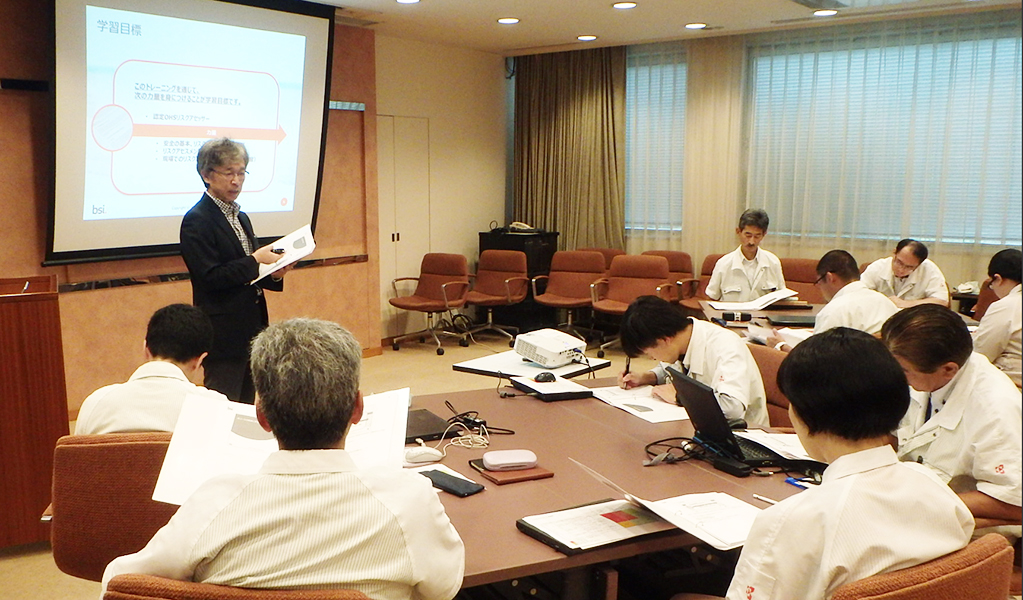
Risk Assessment Competency Improvement
In Japan, risk assessments are conducted by risk assessors. Since last year, we have strived to improve the competence of risk assessors by providing training on machinery safety and effective risk assessment with an external specialist organization to identify risks more effectively. Although the training was held remotely due to COVID-19, we will continue to review our training methods and content. This will help us improve the competence of risk assessment trainers and assessors and help conduct more effective risk assessments to prevent accidents in the future.
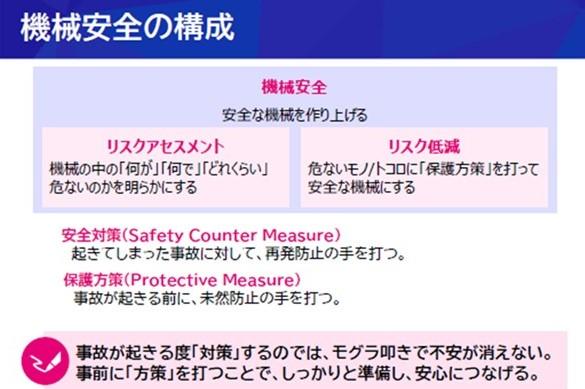
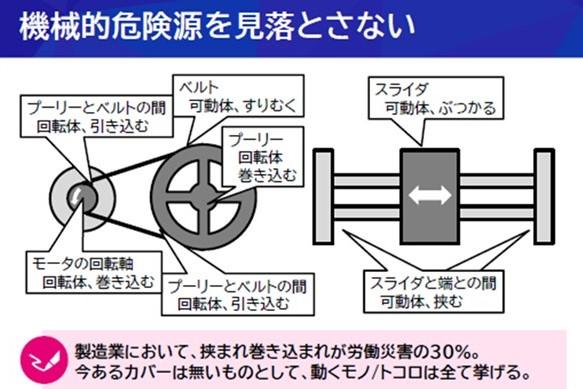
Training Text: Adapted from Japan Certification Corporation's Hazard Identification and Risk Assessment Competency Improvement Education
and Training Textbook
Hazard Awareness Training Using Virtual Reality (VR)
Kyocera Corporation runs hazard awareness training that utilizes VR. Inexperienced employees are given a virtual experience of the dangers inherent in their work. This boosts their hazard awareness and makes them more safety-conscious in their actions. Through this training, we continue improving content and endeavoring to prevent industrial injury and fatalities.
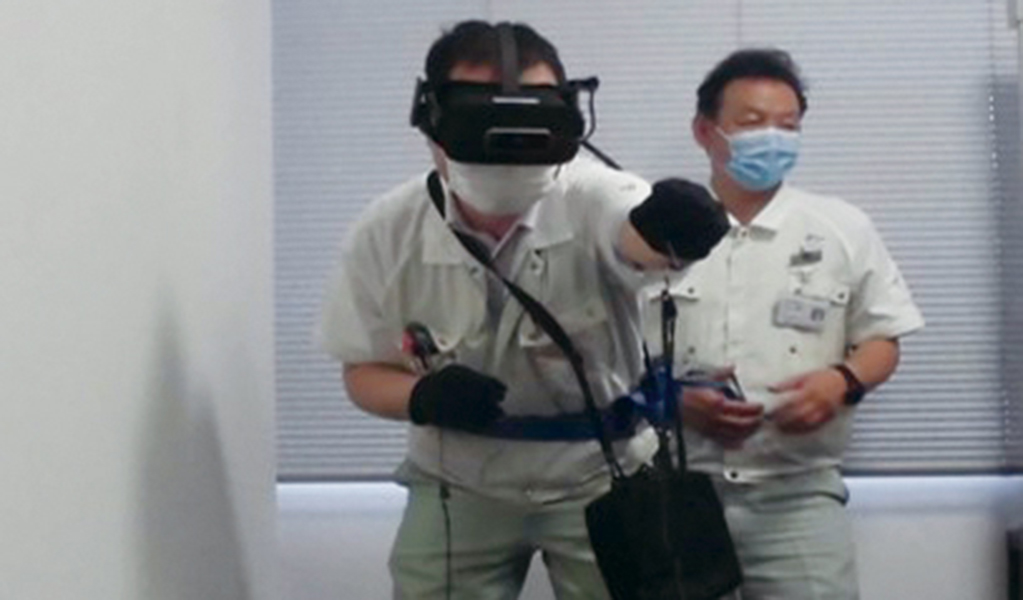
VR hazard awareness training content
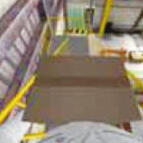
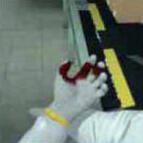
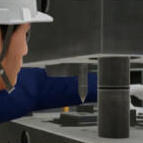
Implementation of emergency measures and training
Kyocera conducts fire drills annually to prepare for fires and other emergencies.
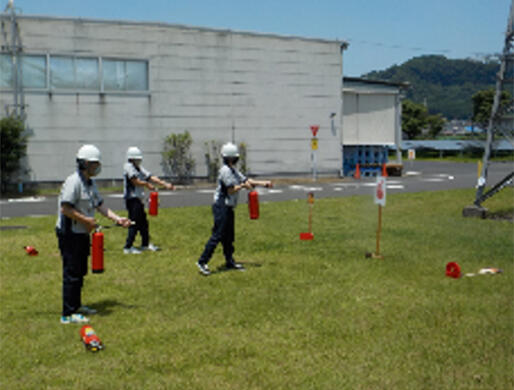
Response to exposure to chemical substances and noise
As an effort to reduce employee risk of exposure to chemical substances in the manufacturing process, we have shifted from a manual transfer method to an automatic supply system using an aired pump. In addition, we have made it mandatory for all employees to wear protective equipment; and to prevent exposure to noise, all employees are required to wear earplugs and other protective equipment.
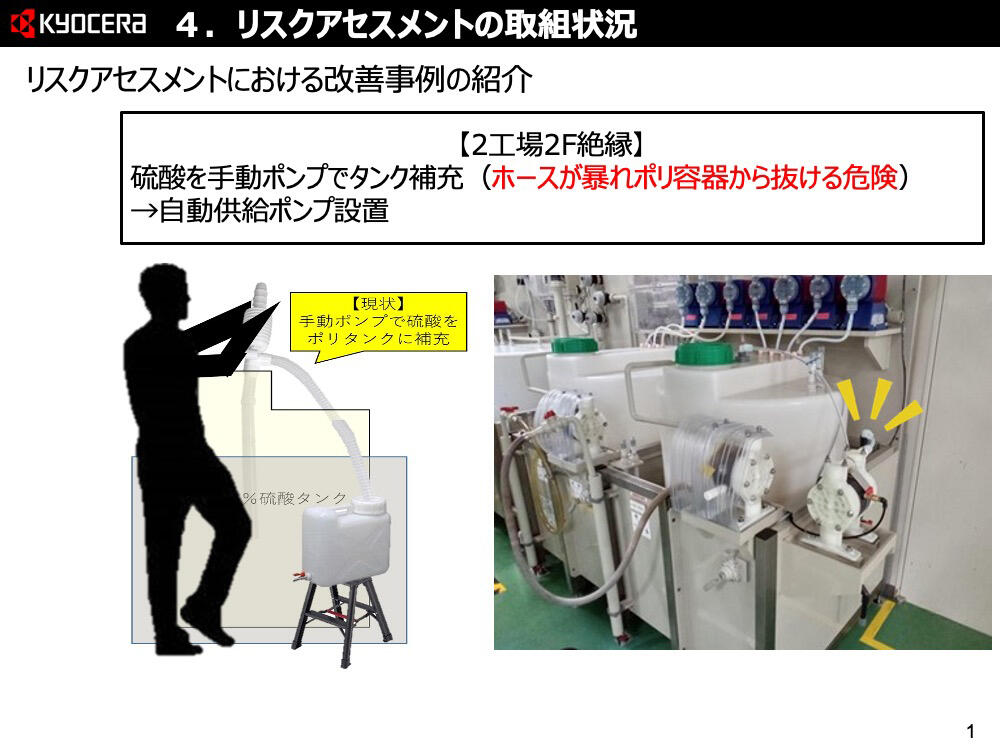
Regular Environmental and Safety Patrols
At Kyocera, plant/office managers and safety managers periodically conduct safety patrols at worksites. In addition to these patrols, the company-wide environmental safety officer conducts an environmental and safety inspection on a regular basis. These activities aim to share risks and issues at worksites and raise employees' safety awareness.
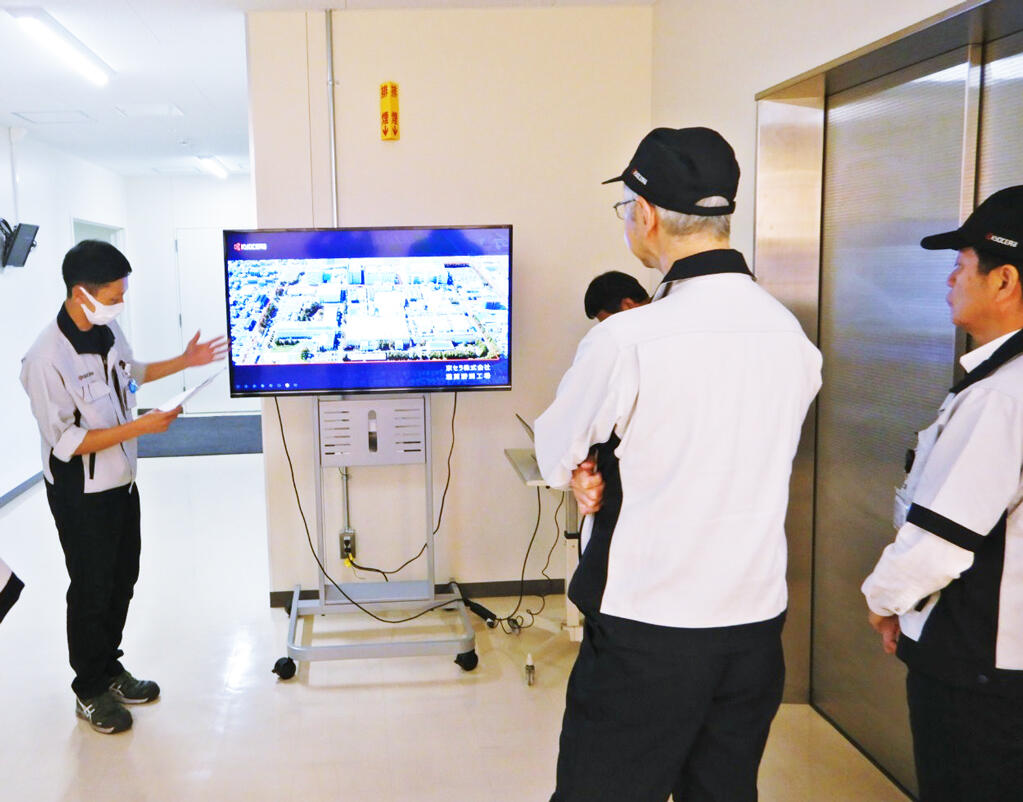
Holding Information Sessions on Workplace Safety
The Kyocera Group regularly holds information sessions about onsite work safety to prevent business partners who enter our sites for service or other related work from being involved in accidents. We hold information sessions to explain campus safety work rules, chemical substance handling, and activities for accident prevention. During these sessions, Kyocera staff and business partners confirmed safety precautions and shared a renewed sense of safety awareness. We will continue to hold briefing sessions to prevent accidents involving our suppliers on our premises.
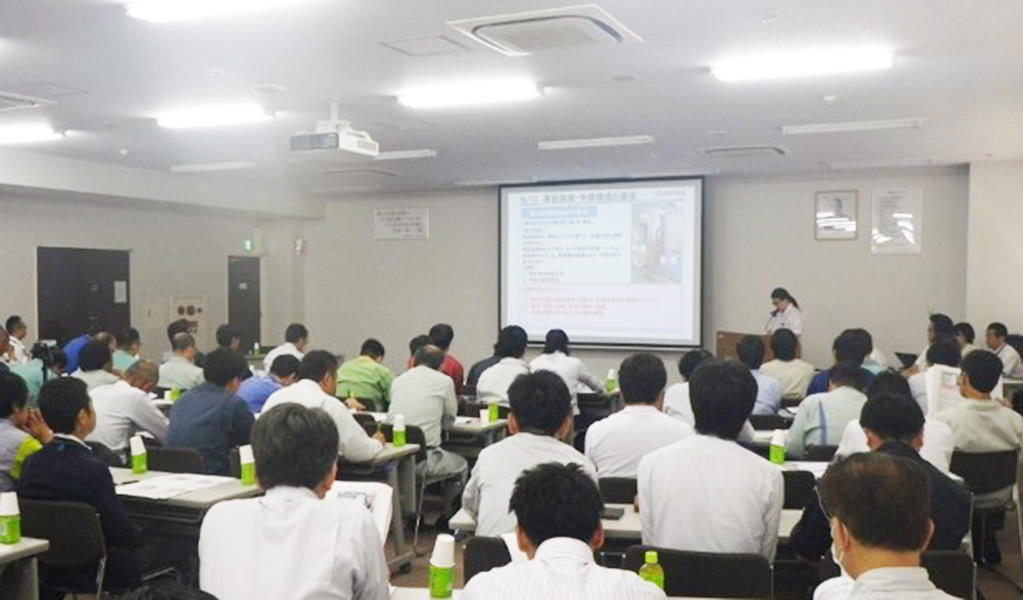
Promotion of Safety and Health Measures Based on Labor-Management Cooperation
The Kyocera Group holds Safety and Health Committee meetings at least once a month for the purpose of smooth and reliable implementation of safety and health management activities at workplaces. During the meetings, the company and labor union cooperate on employee safety and health issues, discussing matters such as the prevention of hazards and health problems, occupational accident reporting and countermeasures, health checkups, safety and health education plans, and other issues.
Deployment of Kyocera Perfect 5S Promotion Activities
The 5S ( Seiri: Sort / Seiton: Set in Order / Seiso: Shine / Seiketsu: Sanitize / Shitsuke: Sustain) is at the heart of work at the Kyocera Group. Aiming to implement 5S activities perfectly at every worksite, Kyocera Perfect 5S Promotion Activities are being introduced globally. Each worksite regularly evaluates the degree of 5S achievement using a company-wide standardized checklist and identifies areas for improvement. Then all members work together to make improvements in the areas identified. 5S training provides an understanding of the objectives and effects of 5S promotion activities. Employees who have completed this training serve as evaluators in order to ensure fair and impartial evaluation and objective judgment. Through these activities, Kyocera aims to create a working environment where every employee can work safely and with peace of mind and to raise each employee's awareness of and commitment to 5S.
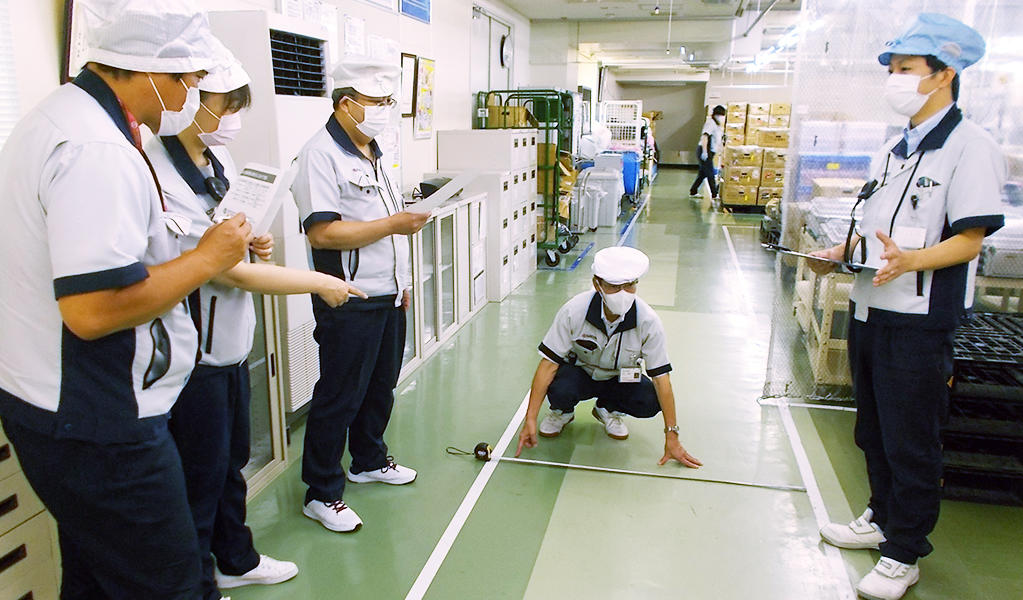