Contribution to the Circular Economy/ Approaches to Waste Reduction
All Kyocera Group corporate activities are based on our corporate motto, "Respect the Divine and Love People," and our three pillars for "LIVING TOGETHER": coexistence with society, coexistence with the global community, and coexistence with nature.
We aim to establish a recycling system that reduces the consumption of natural resources with the goal of protecting the global environment and realizing a sustainable society.
Contribution to the Circular Economy
The Circular Economy Concept
Laws and regulations have been established and standardized with increasing frequency throughout the world. The EU has pioneered the implementation of circular economy action plans, and has actively set goals to reduce the total amount of waste incineration and landfill. In line with these movements, the Kyocera Group established a new division to build a system for the reuse of a wide variety of waste produced at the factories in recycled materials with the goal of achieving zero waste discharge.
Approaches to the Circular Economy
Packaging
Recognizing the urgency of climate change countermeasures, Kyocera is committed to manufacture environment-friend¬ly products and provide them in sustainable packaging.
・Environmental Challenges and Packaging
The Kyocera has adopted a new type of package using a materials-saving design. By reconfiguring the conventional concept of separate internal boxes and partitions within a package, we have developed a single multi-folded cardboard container, reducing materials while maintaining the functionality.
・Recycling of Disposed PET Film
The Kyocera Group maximizes the reduction of PET film waste and minimizes the use of new ingredients by reusing PET film as an ingredient for PET product trays. The company set the goal of using recycled PET film at a level of 50% for trays.
Printer and toner cartridge recycling program
Kyocera Document Solutions Inc., which produces and sells printers and multifunctional peripherals (MFPs), has been working to establish a circular business cycle encompassing product design, production, collection, and recycling.
・Product / Service Design Process
Our product design process includes a wide range of environmental considerations, including durability factors to reduce parts replacement and disposal; 3R factors to "reduce, reuse, and recycle;" and energy efficiency factors to minimize GHG. Products are created using environment-conscious design standards from the initial concept through each stage of development.
・Use of Post-Consumer Recycled (PCR) Materials
We introduce recycled plastics for use in MFPs, dedicated printers, and toner containers, targeting a PCR content of 1% or more for 2023 and 5% or more for 2024 with the ultimate aim of achieving a PCR content of 50% for MFPs.
・From Collection to Reuse
We collect used MFPs and printers in some regions for disassembly and reuse of materials, while cleaning, inspecting, repairing, testing, and reselling units as factory-refurbished equipment. As society calls for transition to a circular econ¬omy, we will expand our product reuse rates while designing products that facilitate easier recycling.
Mobile Phone Recycling Program
Kyocera is promoting recycling to reduce the environmental impact of mobile phones. Mobile phones contain precious resources such as rare metals, gold, and silver, and by promoting recycling, they help prevent environmental destruction through mining and make effective use of resources.
In Japan, Kyocera participates in the Mobile Recycling Network (MRN), which is organized by the Information and Communication Network Industry Association (CIAJ), and carries out collection and recycling activities in cooperation with other companies. Through these efforts, mobile phones manufactured by Kyocera and other companies are collected at a joint collection center for recycling.
Machine Tooling Chips and Chip Case Recycling Program
Kyocera contributes to emission reduction and productivity improvement in factories with a CSR initiative to collect and recycle used carbide materials, chips, and chip cases.
Collecting rare earth elements from fuel cells
As a part of the approaches to sustainable product development and resource circulation, Kyocera has collected used fuel cells from markets and the extraction of rare earth from cell stacks. The development of technology contributes significantly to the recycling of rare earth minerals.
Approaches to Waste Reduction
Resource recovery rate
Until FY2024, Kyocera defined thermally recycled wastes as recyclable wastes. From 2025, in order to promote the circulation of plastics and other resources, Kyocera defines thermal recycled wastes as non-recyclable wastes and strives for reduction. At its five production sites that generate more non-recyclable wastes than other locations, Kyocera places a priority on reduction by setting individual goals.
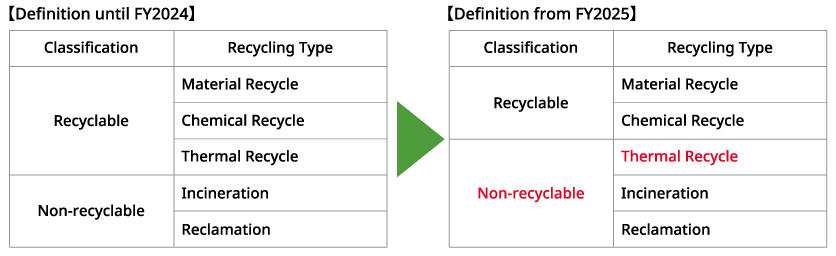
Targets for FY2025 |
|
---|
According to the previous definition (including thermal recycling as a category of recyclable waste), recycling ratio by the Kyocera Group (Japan) in FY2023 was 99.7%.
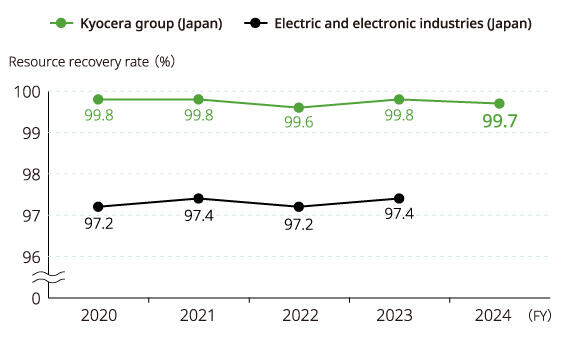
The definition of the recycling rate (%) is "1 - final disposal amount/discharge amount" x 100.
Recycling rates have not been provided for the four main electric and electronic goods industry bodies for FY2023 and have been omitted.
Waste Discharge
The Kyocera Group manages the amount of waste discharged and disposed of in landfills from the viewpoint of resource recycling. We evaluate the amount of waste discharged, the unit cost of waste treatment, and the risks of treatment contractors at our production sites.
As a result of the FY2025 waste risk assessment, there were 7 sites with high waste risk, and the total amount of waste discharged was 23,600 tons, accounting for 57% of the total amount of waste discharged in FY2024.
Targets for FY2024 |
|
---|---|
Achievements in FY2024 |
|
Targets for FY2025 |
|
---|
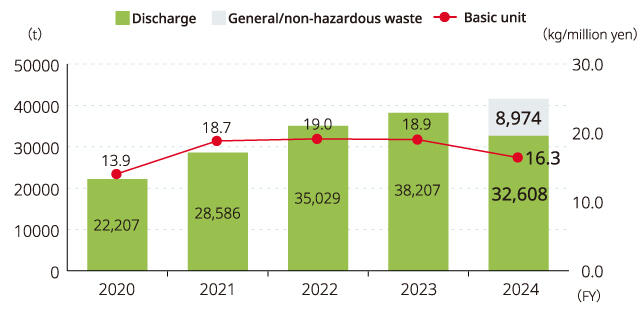
Range of Waste to be Recycled
FY2020~2023:[Japan] Industrial Waste+ Specially Controlled Industrial Waste [Overseas] hazardous waste
FY2024:[Japan]Industrial Waste+ Specially Controlled Industrial Waste + General Waste [Overseas]Hazardous waste+ Non- hazardous waste
Data in FY2023 has been updated to improve the accuracy of data aggregation at some locations.
Cases of Waste Reduction
Reduction of industrial waste by volume reduction of grinding waste liquid
The Kagoshima Kokubu Plant implemented forced air evaporators to evaporate water content from polishing waste liquid, which leads to the reduction of waste liquids and the overall reduction of industrial waste. The plant uses waste heat to increase the temperature of the forced air evaporators.
Total Waste Reduction: 458 t/year*
Total amount of reduction by 2 units is shown. (1 unit was implemented in FY2023).
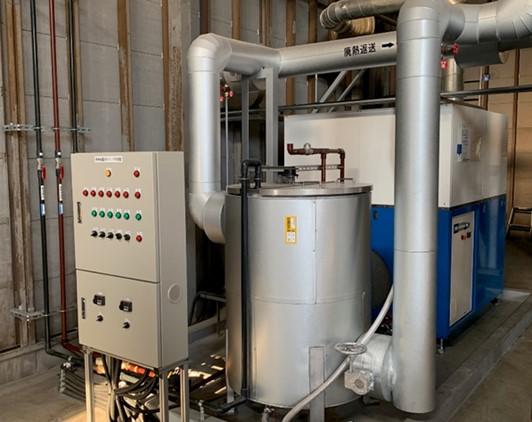
Reduction of Industrial Waste by Implementation of Fenton Pre-treatment Equipment
The Kyoto Ayabe Plant implemented Fenton pre-treatment equipment to process wastewater containing high-concentrations of organic substances. Before implementation, the plant was unable to process concentrated wastewater using previous water treatment methods, forcing disposal as industrial waste. Implementation of the Fenton pre-treatment equipment allows the plant to process concentrated wastewater using currently available methods, which reduces the discharge of industrial waste.
Total Waste Reduction: 676 t/year
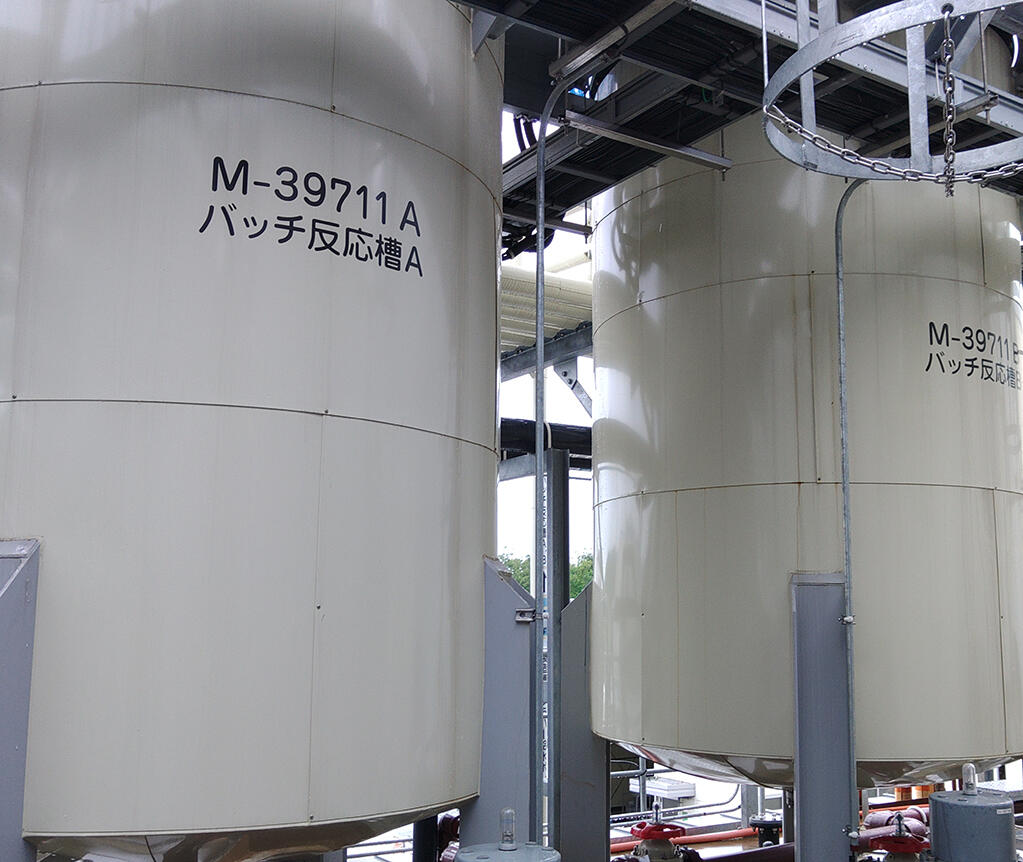
Reduction of industrial waste by volume reduction of grinding waste liquid
KYOCERA OPTEC (DONGGUAN) CO., LTD. reduced its industrial waste by installing centrifuges for its lens manufacturing process, which allow polishing solution to be reused by separating out impurities.
Total Waste Reduction: 120 t/year
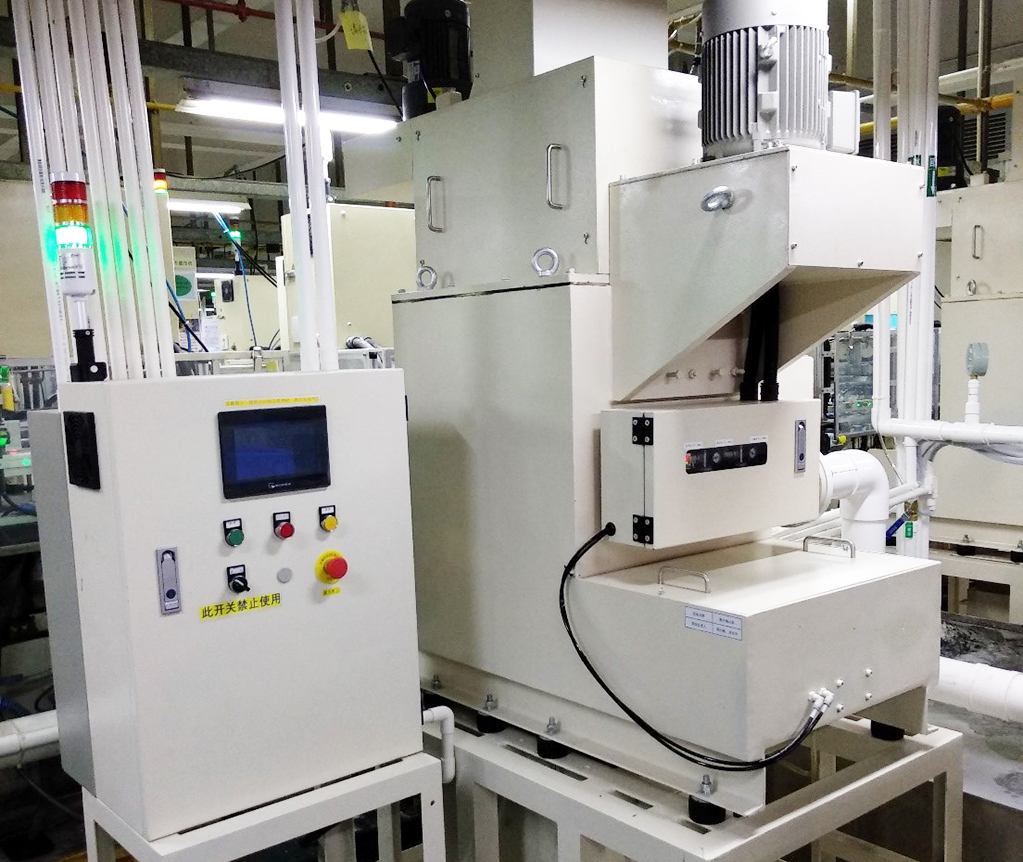
Corporate Motto / Management Rationale / Management Philosophy
- Top Management Message
- Sustainability Management
- Kyocera Group CSR Guidelines
- Stakeholder Engagement
- Environmental Safety Policy / Targets and Promotion System
- Measures to Fight Climate Change -Information Disclosure Based on TCFD Recommendations-
- Water Risk Response
- Contribution to the Circular Economy/ Approaches to Waste Reduction
- Initiatives to Prevent Environmental Pollution
- Biodiversity Conservation
- Environmentally Friendly Products / Green Procurement
- Environmental Communication
- A History of Our Environmental Protection Activities
Social Citizenship Initiatives
- The Kyocera Group Human Capital
- Respect for Human Rights
- DEI Promotion
- Occupational Safety
- Occupational Health, Safety, and Fitness Initiatives
- Supply Chain Management
- Approaches to Raising Quality and Customer Satisfaction Levels
- Social Contribution Activities
- Academic Advancement and Research
- Support for Culture and the Arts
- International Exchanges and Collaboration
- Environmental Protection Activities
- Local Community Activities
- Social Welfare Activities
- Contributions to Society through Business Activities