Silicon nitride is an outstanding engineering ceramic that possesses superior heat shock resistance and corrosion resistance, as well as high strength and fracture toughness even at high temperatures.
Kyocera's silicon nitride achieves high strength and thermal conductivity due to our unique processing technology*, and is widely used as a highly reliable structure.
In particular, our high thermal conductivity silicon nitride (SN241O) has twice the thermal conductivity of our conventional silicon nitride (SN240O) and possesses excellent thermal shock resistance.
For this reason, our high thermal conductivity silicon nitride is used as a protective tube for heat sources, such as electric heaters and gas-fired burners, thereby contributing to the promotion of energy conservation and CO2 reduction.
*According to research by Kyocera (as of July 25, 2022)
Features
- High Thermal Conductivity 54W/m・K
Twice the thermal conductivity of our conventional material (SN240O) - High Heat Shock Resistance Δt=900°C
Reduced risk of damage due to heat shock - High Corrosion Resistance to Molten Metal
Low reactivity with molten metal (high corrosion resistance) and low wettability (difficult to adhere)
Application Examples
Usage Example as a Heater Tube (Protective Tube) for a Molten Aluminum Holding Furnace
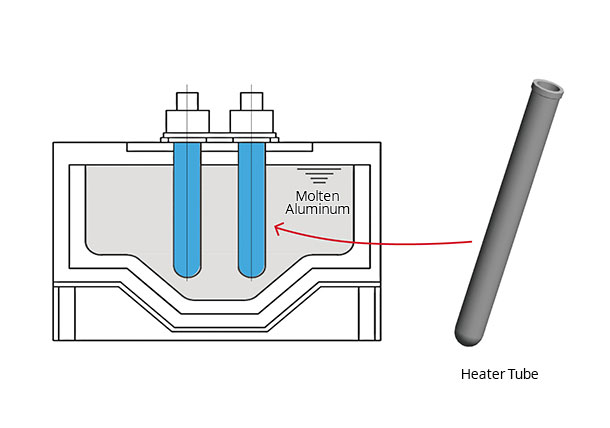
Achievement of Energy Saving
High thermal conductivity silicon nitride (SN241O) can achieve high thermal efficiency.
For example, when trying to maintain 5 tons of molten aluminum at 730°C, the heater temperature can be set lower compared with the conventional silicon nitride SN240O. This reduces energy consumption. The table below is an example.
Material | Molten Aluminum Temperature | Temperature Inside the Heater Tube | Δt |
---|---|---|---|
Silicon Nitride SN240O |
730℃ | 930℃ | 200℃ |
High Thermal Conductivity Silicon Nitride SN241O |
730℃ | 880℃ | 150℃ |
* Δt = [Temperature Inside Heater Tube] - [Temperature of Molten Aluminum]
Comparison of Thermal Conductivity
Comparison with Kyocera's Conventional Silicon Nitride and Other Companies' Silicon Nitrides for Structural Components
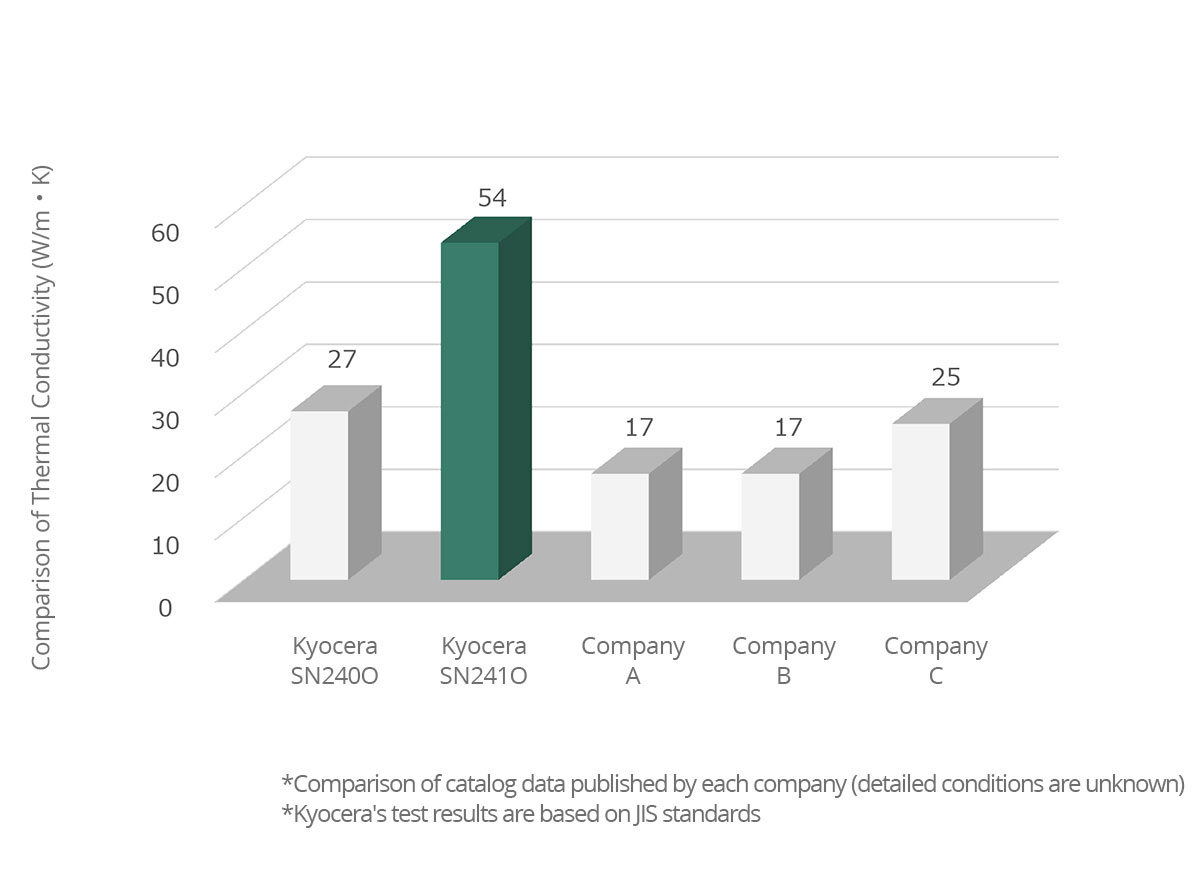
Video (31 seconds)
We placed two pieces of silicon nitride of the same thickness on a heated hot plate. We then placed candles on top of the silicon nitride in order to visually confirm the difference in heat transfer speed (thermal conductivity) between our conventional material (SN240O) and high thermal conductivity silicon nitride (SN241O).
High Corrosion Resistance to Molten Metal
Silicon nitride ceramics have low reactivity with molten metal (high corrosion resistance) and low wettability (difficult to adhere).
It can also be used for molten aluminum for long periods of time due to its high strength at high temperatures.
Wettability Test Results
Test Conditions :
We placed ADC12 (aluminum alloy) on plates made from each material, heated them to 1,000°C (vacuum), and then cooled.
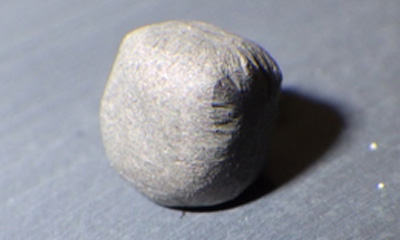
Kyocera Silicon Nitride (SN241O)
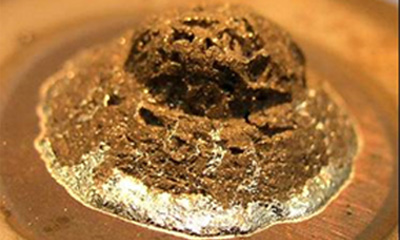
SKD Material (Metal)
Property Data Comparison
Comparison of major properties between Kyocera's conventional silicon nitride (SN240O) and high thermal conductivity silicon nitride (SN241O)
Material Material Code |
Silicon Nitride | ||||
---|---|---|---|---|---|
SN241O | SN240O | ||||
Color | Black | Black | |||
Density | g/cm3 | 3.2 | 3.3 | ||
Mechanical Characteristics | Vickers Hardness HV9.807N | GPa | 13.8 | 14.0 | |
Flexural Strength (3-point Bending) | MPa | 790 | 1,020 | ||
Young’s Modules | GPa | 290 | 300 | ||
Poisson's Ratio | - | 0.28 | 0.28 | ||
Fracture Toughness (SEPB) | MPa・m1/2 | 6-7 | 7 | ||
Thermal Characteristics | C.T.E | 40~400℃ | × 10-6/K | 2.9 | 2.8 |
40~800℃ | 3.5 | 3.3 | |||
Thermal Conductivity | 20℃ | W/(m・K) | 54 | 27 | |
Specific Heat Capacity | J/(g・K) | 0.66 | 0.65 | ||
Thermal Shock Temperature Difference (Put in Water, Relative Method) | ℃ | 900 | 800 |
Are you considering cost reduction through high thermal efficiency, replacement frequency reduction, or promotion of sustainable business through CO2 reduction?
Contact us for a free consultation with one of our product solution experts.
Values are based on typical material properties and
may vary according to product configuration and manufacturing process.