New solution for achieving complex shapes while reducing raw material waste
Slurry conditioned material is casted into product-shaped mold and formed by solidification.
This is Kyocera's new forming method which enables near-net shapes, and is expected to expand ceramics' applications further.
Parts developed via F-Molding have the same or better characteristics compared to those produced by CIP (Cold Isostatic Pressing) forming.
Features
- Unique and Complex Shaped Part FormingAchieves complex designs which can not be achieved by conventional green machining and grinding.
- Near-Net Shape FormingCost savings achieved by reducing material waste with less machining (compared to CIP forming)
- Small Volume Orders AvailableInitial cost saving with less expensive mold (compared to injection molding and press forming)
Design Samples
Material: Zirconia (ZO 206 N) Size: Φ 50 mm
Material: Silicon Nitride (SN 240 O) Size: Φ 50 mm
*Please ask us about available sizes.
Manufacturing Process
Conventional Method
CIP forming +
Green machining
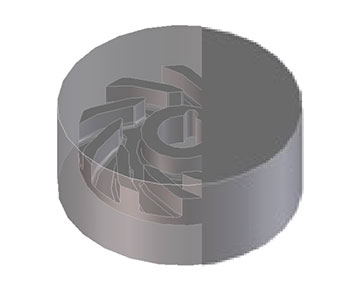
Forming a cylindrical ceramic block
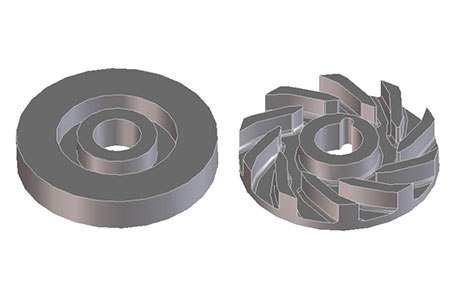
Green Machining into shape
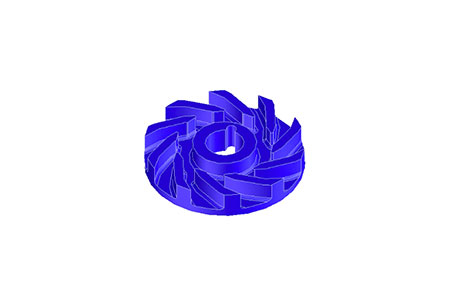
After sintering, final grinding
New Method
F-Molding
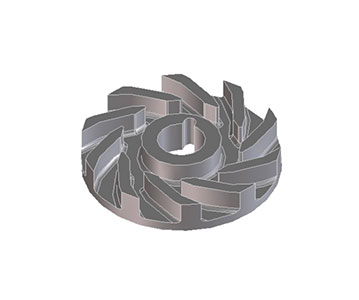
Molding into near-net shape
- No green machining process
- ・Reduction of raw material waste
・Reduction of processing time
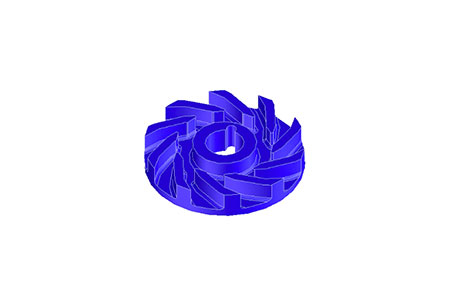
After firing, final grinding
Material Lineup
Material Material Code |
Zirconia | Cordierite | Silicon Nitride | ||||
---|---|---|---|---|---|---|---|
ZO206N | CO220O | CO720O | SN240O | ||||
Color | - | White | Gray | Gray | Black | ||
Density | g/cm3 | 6.0 | 2.50 | 2.54 | 3.3 | ||
Mechanical Characteristics | Vickers Hardness HV9.807N | GPa | 12.0 | 8.0 | 8.5 | 14.0 | |
Flexural Strength (3-point Bending) | MPa | 1,100 | 190 | 200 | 1,020 | ||
Young’s Modulus | GPa | 210 | 140 | 145 | 300 | ||
Poisson’s Ratio | - | 0.32 | 0.31 | 0.31 | 0.28 | ||
Fracture Toughness (SEPB) | MPa・m1/2 | 6 | 1-1.5 | 1-1.5 | 7 | ||
Thermal Characteristics | Coefficient of Linear Thermal Expansion | 40-400℃ | × 10-6/K | 10.4 | (*) 1.5 | (*) 1.5 | 2.8 |
40-800℃ | 10.8 | (*) 2.1 | (*) 2.1 | 3.3 | |||
Thermal Conductivity | 20℃ | W/ (m・K) | 3 | 4 | 4 | 27 | |
Specific Heat Capacity | J/ (g・K) | 0.44 | 0.71 | 0.74 | 0.65 | ||
Thermal Shock Resistance (quenching into water) |
℃ | 300 | 450 | 400 | 800 |
* <|0.05|(23℃)、<|0.02|(22℃)
Materials not listed in the table are under development, please feel free to contact us for further information.
Values are based on typical material properties and
may vary according to product configuration and manufacturing process.