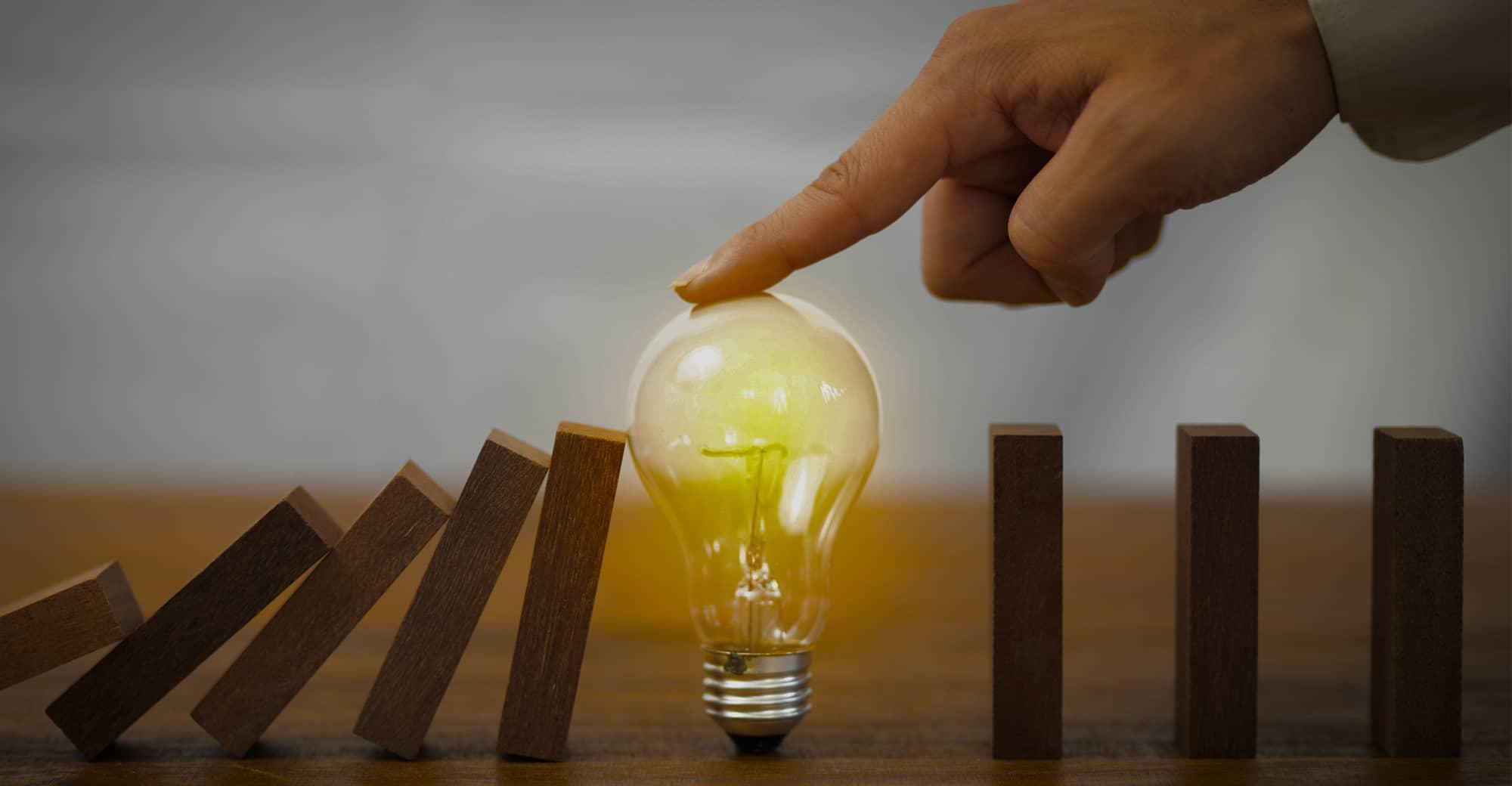
Case Study for Aluminum Casting Part Replacement with Fine Ceramics to Improve Productivity and Quality
*Low-pressure casting is a casting method for manufacturing aluminum products by pressurizing the inside of a closed furnace to push up the molten aluminum through a stalk, and then pouring the molten metal into a die.
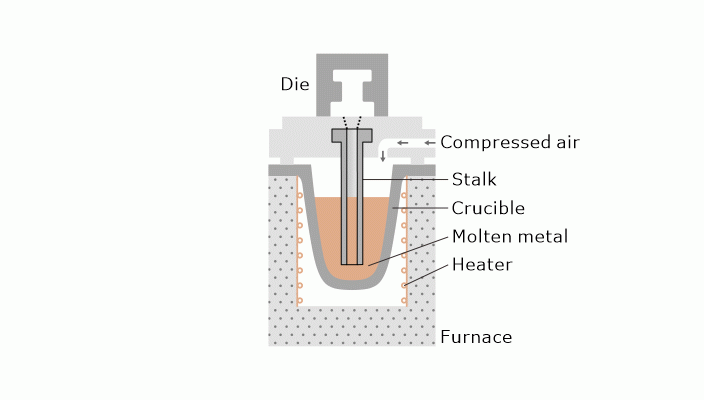
We considered the use of a ceramic stalk to improve productivity and quality.
Cast iron stalks tend to become wet with molten aluminum, which results in a significant amount of adherence to the pipe walls. Consequently, it was necessary to stop the line to perform maintenance procedures such as removing deposits.
Additionally, in order to prevent melting damage of cast iron stalks due to molten aluminum, it was necessary to replace the stalk once every two weeks. This resulted in low productivity.
Furthermore, because the molten aluminium eroded the cast iron, the molten aluminum became contaminated with impurities.
Conditions
・Material must be able to withstand high temperatures.
・Material must not be corroded by molten aluminum.
・Material must be resistant to the adherence of molten aluminum.
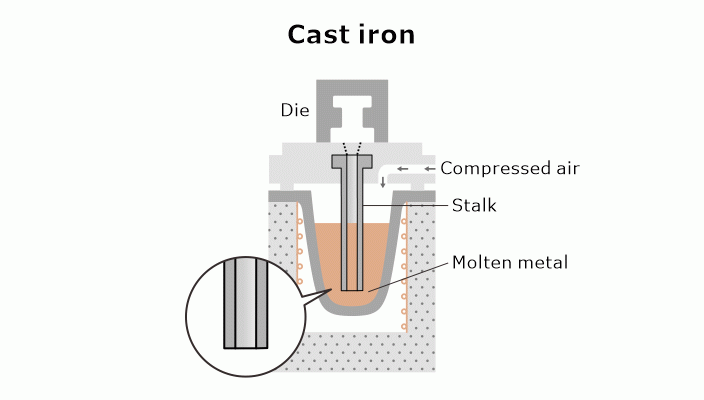
We changed the material from conventional cast iron to Fine Ceramics (silicon nitride), which has high heat and corrosion resistance.
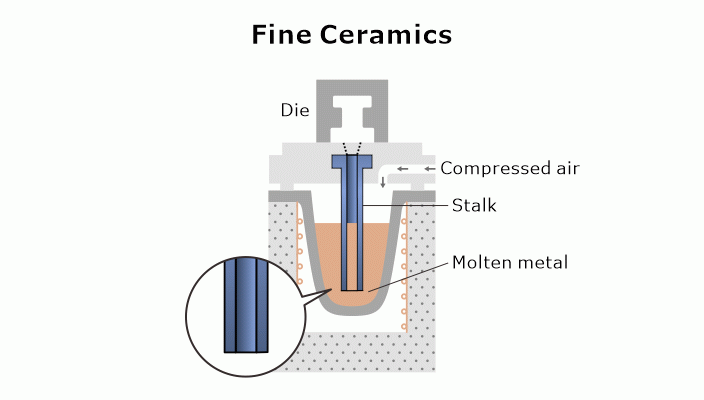
By changing from cast iron to Fine Ceramics with high heat and corrosion resistance, we succeeded in extending the lifespan of low-pressure casting stalks and improving productivity.
Until now, it had been necessary to replace parts once every two weeks, but parts are now replaced once every one to three years. Furthermore, we were able to reduce the burden of daily maintenance (removal of deposits) by decreasing the amount of deposits.
Since Fine Ceramics possess outstanding corrosion resistance, we were able to eliminate impurities resulting from molten aluminum erosion, which occurred when using a cast iron stalk. As a result, the customer was able to manufacture higher-quality cast parts.
Also, the specific gravity of silicon nitride is about 50% lower than cast iron. This makes it easier to handle the stalk during maintenance and replacement.
Moreover, since silicon nitride has lower thermal conductivity compared to cast iron, it has less heat dissipation to the outside, and energy loss was reduced.
* Values are based on the usage results at the customer who actually purchased the product.
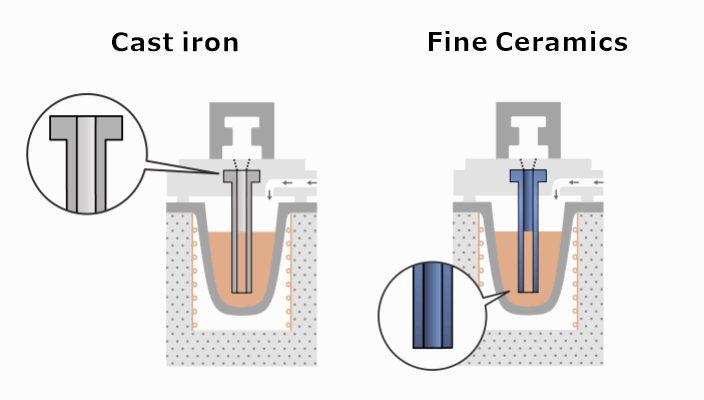
*Material property can change depending on operating conditions.