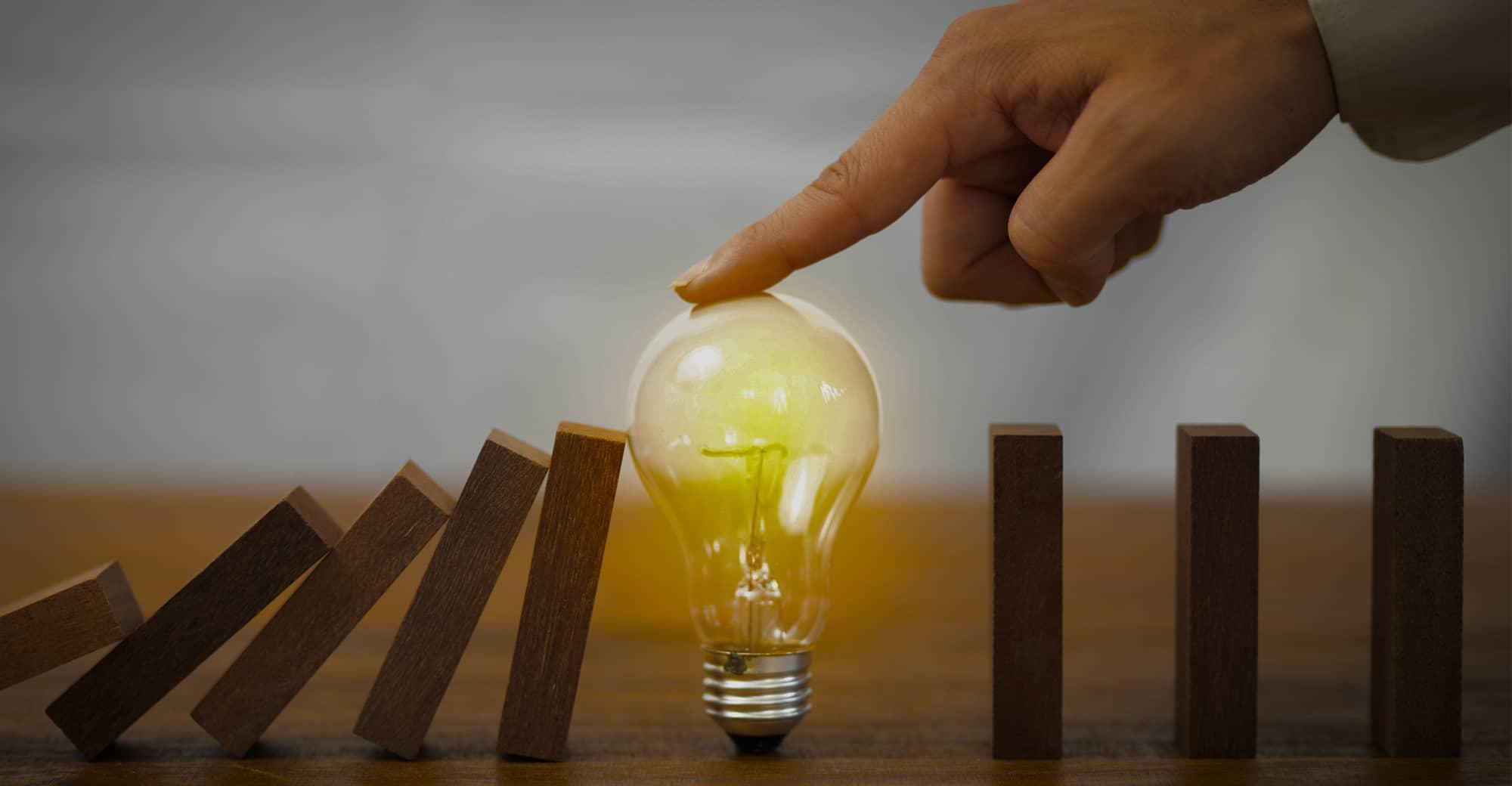
Example of improving dimensional accuracy with a zirconia plate of low thermal expansion and thickness tolerance of +/-10 micrometers.
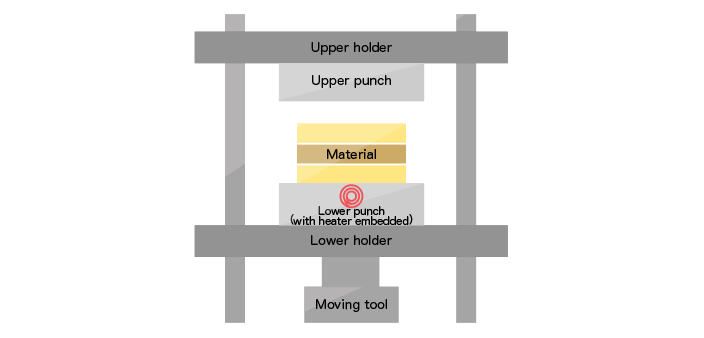
A thermal insulator made of a cement material was conventionally used for the tooling holders. However, there was a deformation issue of the lower punch caused by thermal expansion of the supporting holder with an embedded heater whose temperature reached up to 400 degrees Celsius. The deformation of the lower punch resulted in larger thickness variation of the components and poor yield.
Conditions
・Low thermal expansion at high temperature of 400 degrees Celsius
・Low thermal conductivity to insulate the entire machine from the embedded heater
・High hardness and stiffness as the tooling holder
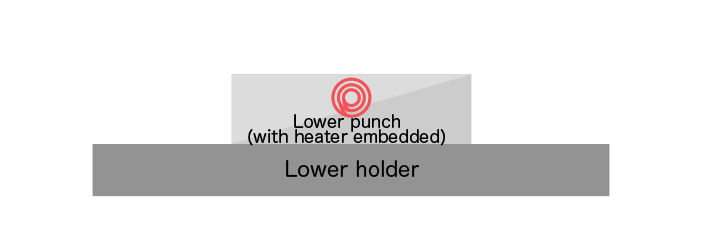
We used zirconia with its lower heat expansion compared to conventional thermally insulating cement material.
The zirconia was worked at a high degree of accuracy to a set plate shape (thickness accuracy ±0.01mm), and installed as mountings for the molds (heat conductivity, hardness, and strength tolerances checked with samples).
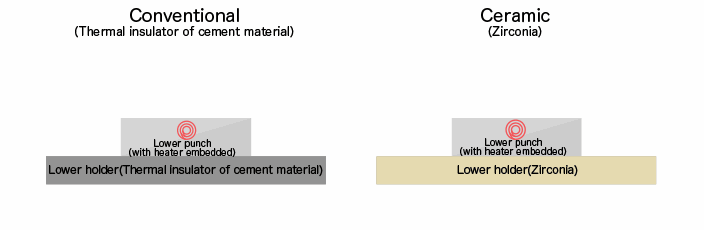
By reducing thermal expansion of the tooling holder, we significantly improved accuracy of the tooling punch. This enabled the client to produce multilayered components of higher dimensional accuracy than before.
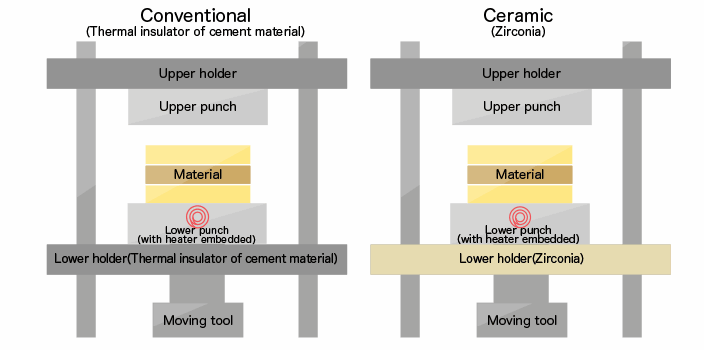
*Material property can change depending on operating conditions.