"Sensing", "Filtering", "Resetting by heating" – Kyocera’s Porous Alumina Heater can fulfill all these different actions at the same time. Here we speak with one of Kyocera’s engineers about developing this product from scratch. Through many development challenges and after much effort, the potential of this porous alumina heater is now beginning to be realized.
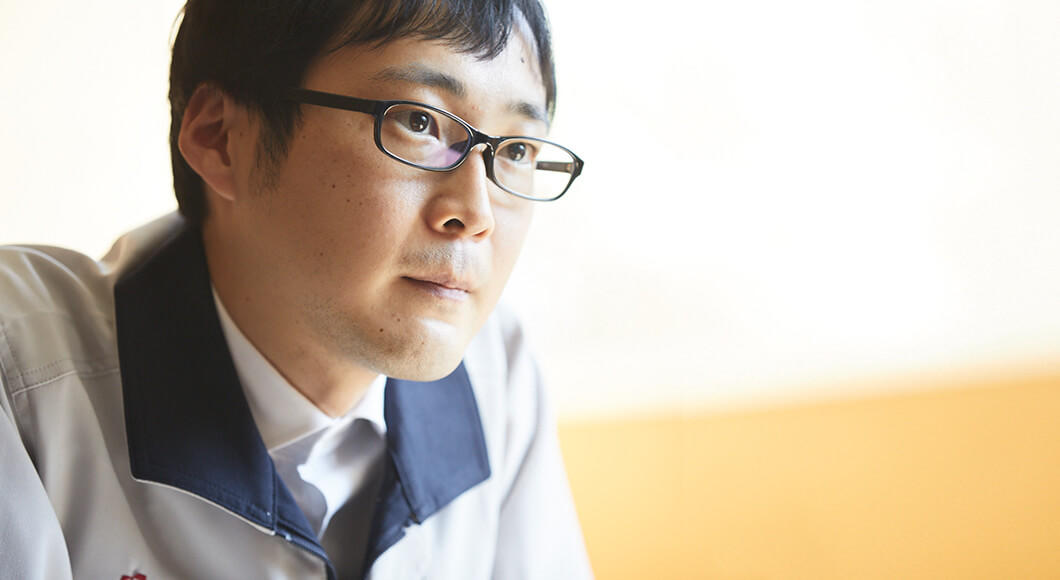
Start development from zero know-how
Could you explain about the ceramic heater from the beginning?
Kyocera has more than 30 years of experience in developing ceramic heaters. Our heaters are made using two primary types of materials. One type is made from Silicon Nitride. Because it can reach temperatures of 800℃ nearly instantly, it is used as an ignition assist in diesel engines. The other type is made from Alumina and is used in hair irons and bidet toilet seats. Ceramic heater development has been evolving over the years, and one such heater we developed was the Porous Alumina Heater.
How does it work?
The porous filter performs a sensing function while catching particles, and when a certain particle limit is exceeded, the ceramic heater is activated to burn the particles in a heating process known as resetting. Put simply, the Porus Alumina Heater is a combination of a porous filter and a ceramic heater.
Does Sensing, Filtering, and Resetting (heating) occur simultaneously?
Yes. To be honest, I thought it could be impossible at the beginning of this project. It something that no one had done before, so we were starting from zero.
How did you accomplish that?
At first, I started by speaking with other departments and gathering information. We already had a lot of knowledge about heaters, but we weren’t familiar with how to integrate porous materials. I got tips from various departments within Kyocera and slowly put them together one-by-one as I proceeded.
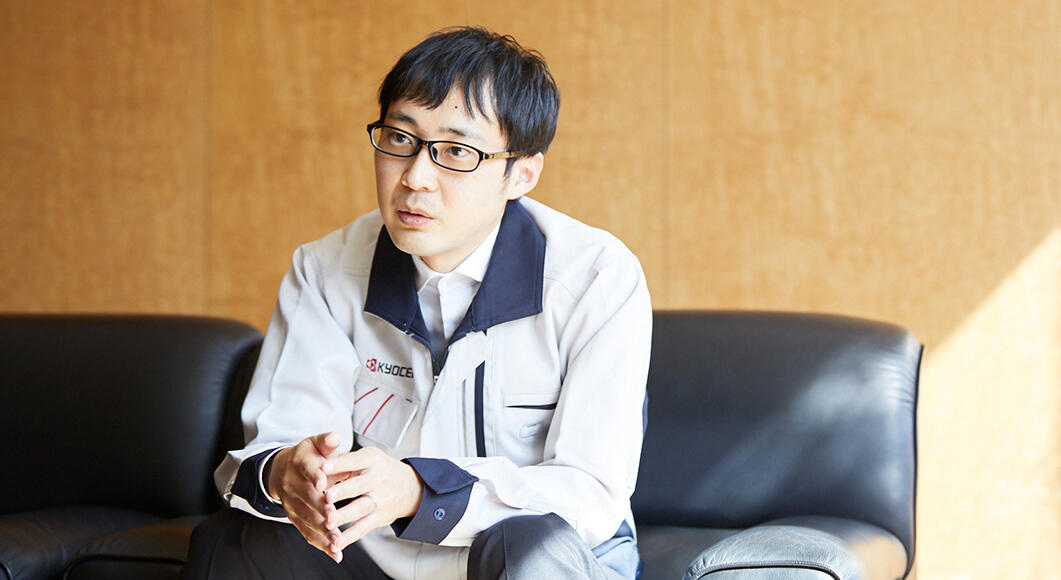
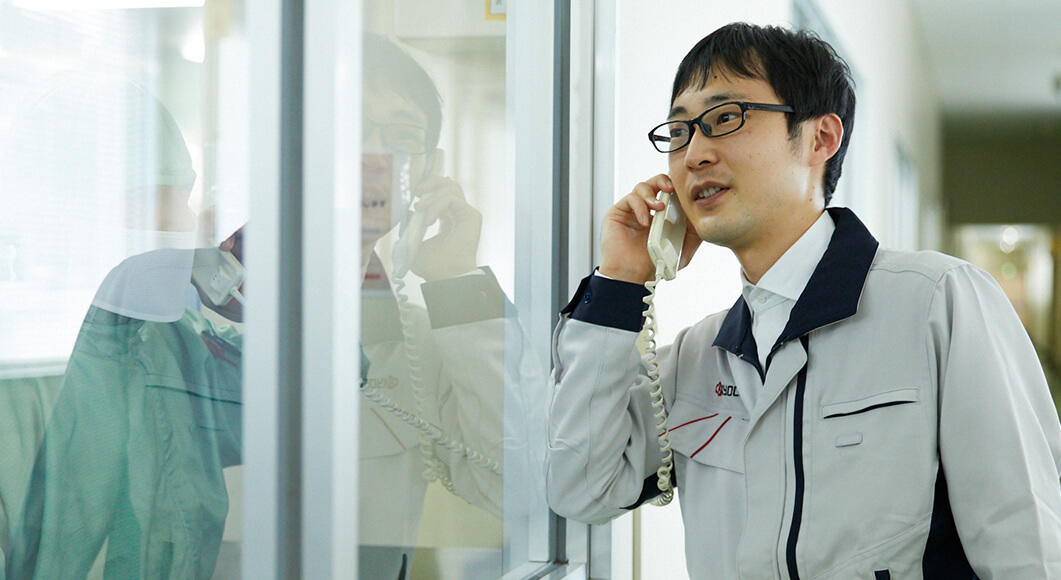
Potential of the Porous Alumina Heater
What was the most challenging part of development?
The materials exhibited cracking errors between the porous filter layer and the ceramic heater layer due to different shrinkage rates and these cracks occurred during the sintering process. Generally, raw ceramic powder material is kneaded into a sheet and then stacked. However, during the sintering process, the material shrinks slightly. Since the porous filters and the ceramic heaters have different properties, there was cracking at the interface. In order to solve this problem, we had to define the most appropriate sheet sizes and adjust the kinds of additives and the blending ratio of the material.
It seems like it was a mind-boggling operation, wasn’t it?
Yes, it was. We didn't have the know-how to make a porous filter at the beginning, so it was difficult to achieve both the strength and the filter functions. The structure has to be a hollow shape to allow gas to pass through in order to catch particles.
So it was a typical trade-off situation?
Yes, I thought so. However, we kept trying and made errors every day. There was a design team, a sample production team, and an evaluation team and we all contributed as much as we could.
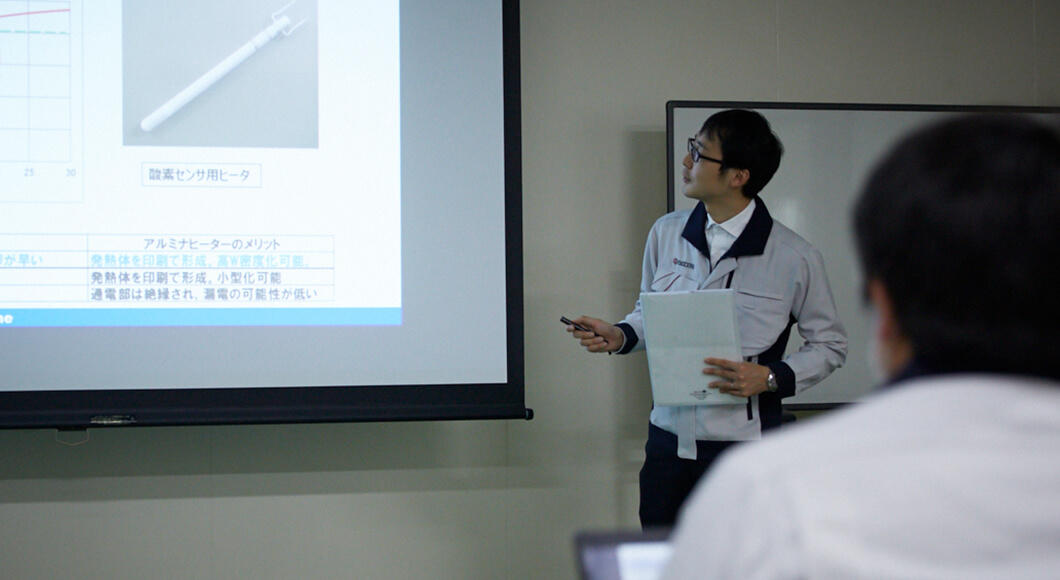
Did you have to repeatedly make hypotheses and conduct tests?
Yes, I did. I think it is important to do hypothesis and test cycles, then problems can be solved little by little. It was the result of gathering knowledge from many specialists from various fields.
It is a demonstration of Kyocera's strengths that you could put together such a team. Where will the porous filter be used in the future?
We originally developed it as a sensing application, so I would like to contribute to various markets where sensors are applied. Throughout the world, sensors are installed in various places to collect information and take action, so I think it could be used for applications such as heater self-regeneration and detection.
Can it also be used for humidity sensors?
Yes, it can. Water droplets instead of particles can also be collected by the filter. Other potential applications include self-regenerative filters and self-activating catalysts. We have been involved with heaters for a long time, and I hope that we will be able to develop heaters that add value through sensing functions, just like this porous alumina heater. I think that we are still at the starting point for ceramic heater innovations. We plan to actively take on difficult challenges and further enhance our technological capabilities. I would be happy if anyone could contact us to share their ideas.
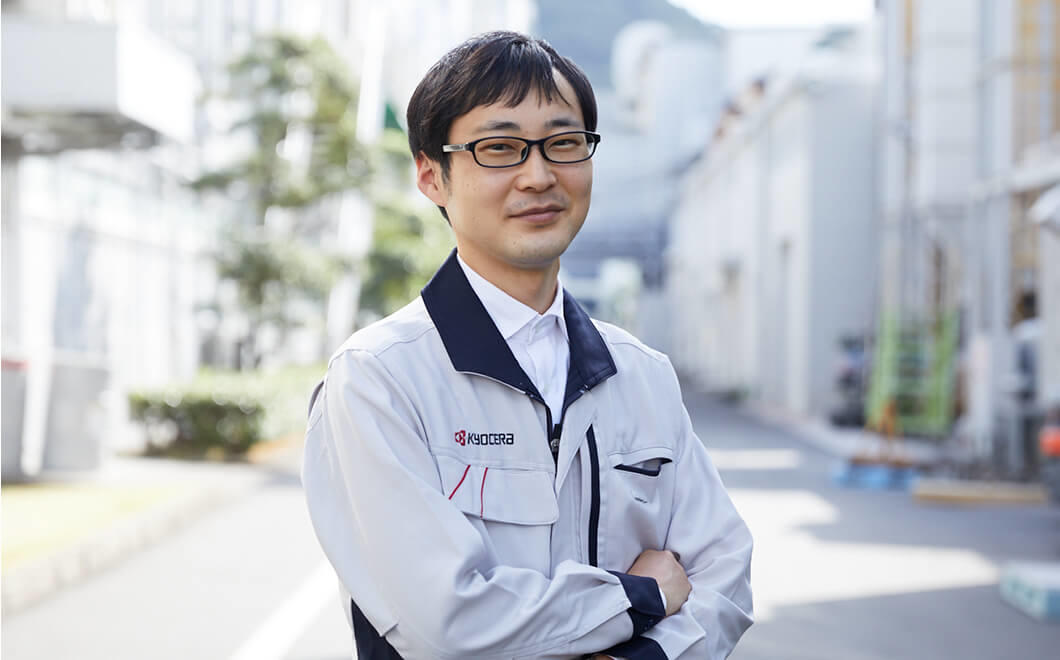