Aiming for maximum quality in a "micro world"
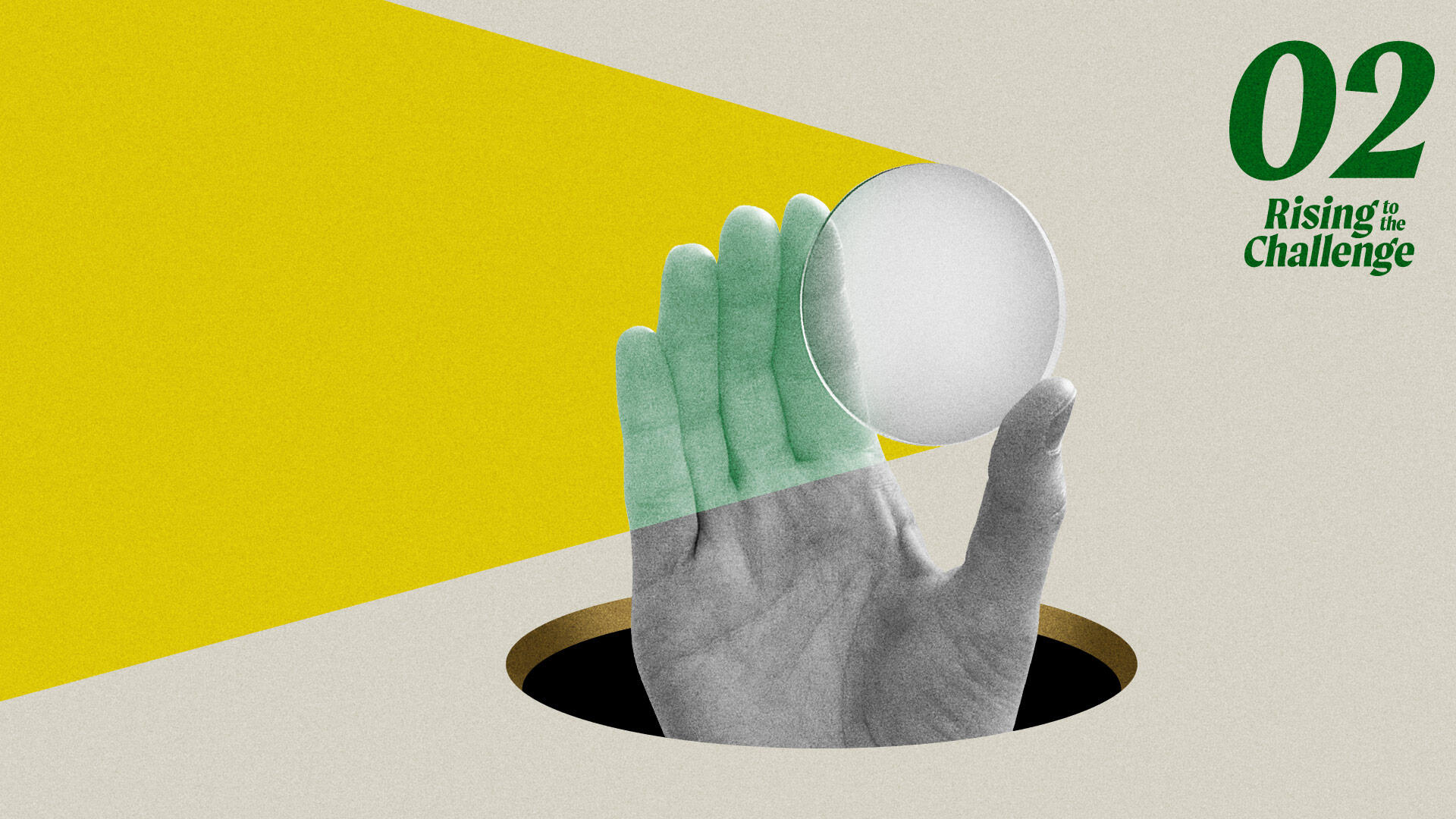
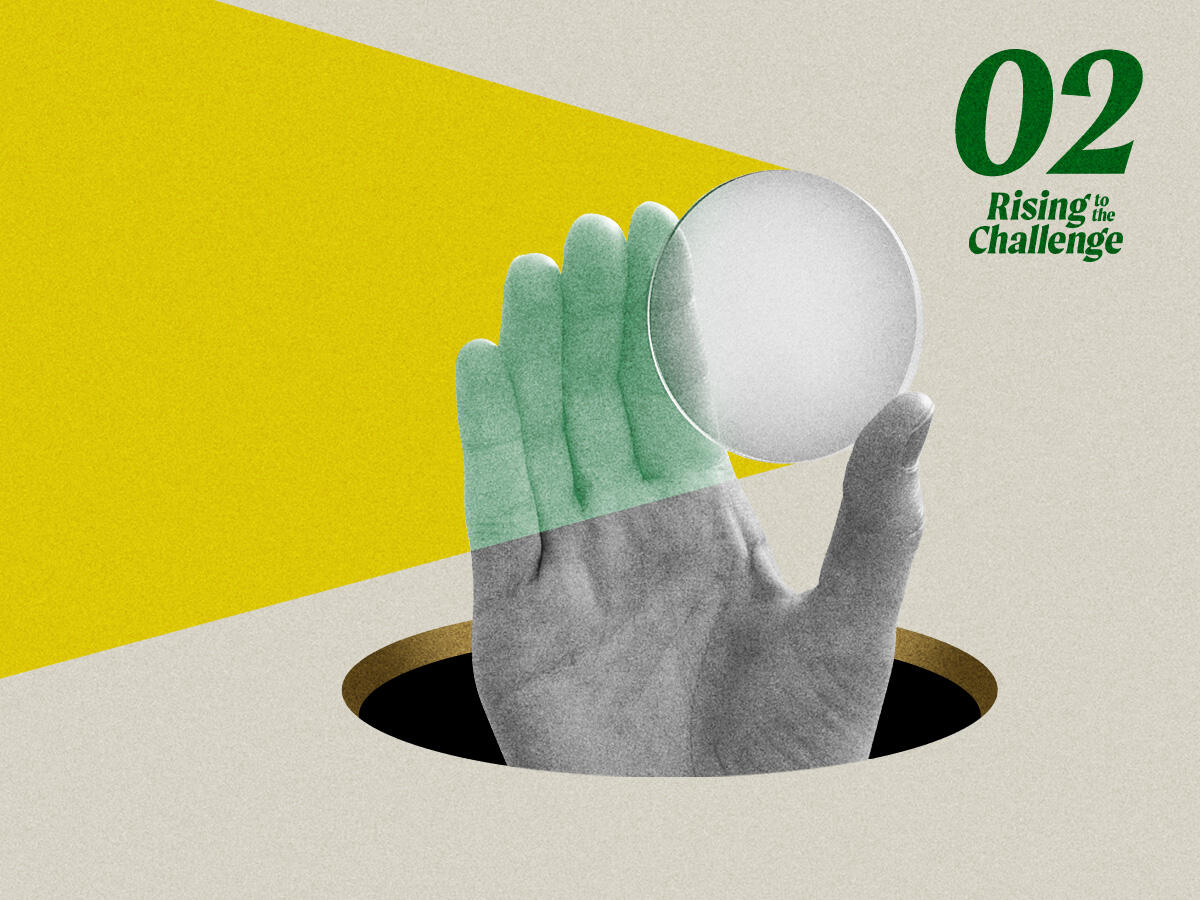
Quality control is an inevitable concern for manufacturers. If quality falters, there may be not only financial losses but, in some cases, it could result in social disruption or a major accident. What are the chances that the products you are working on will be defect-free? Kyocera’s engineers are dedicated to quality improvement every day.
An inquiry about models that had already been delivered.
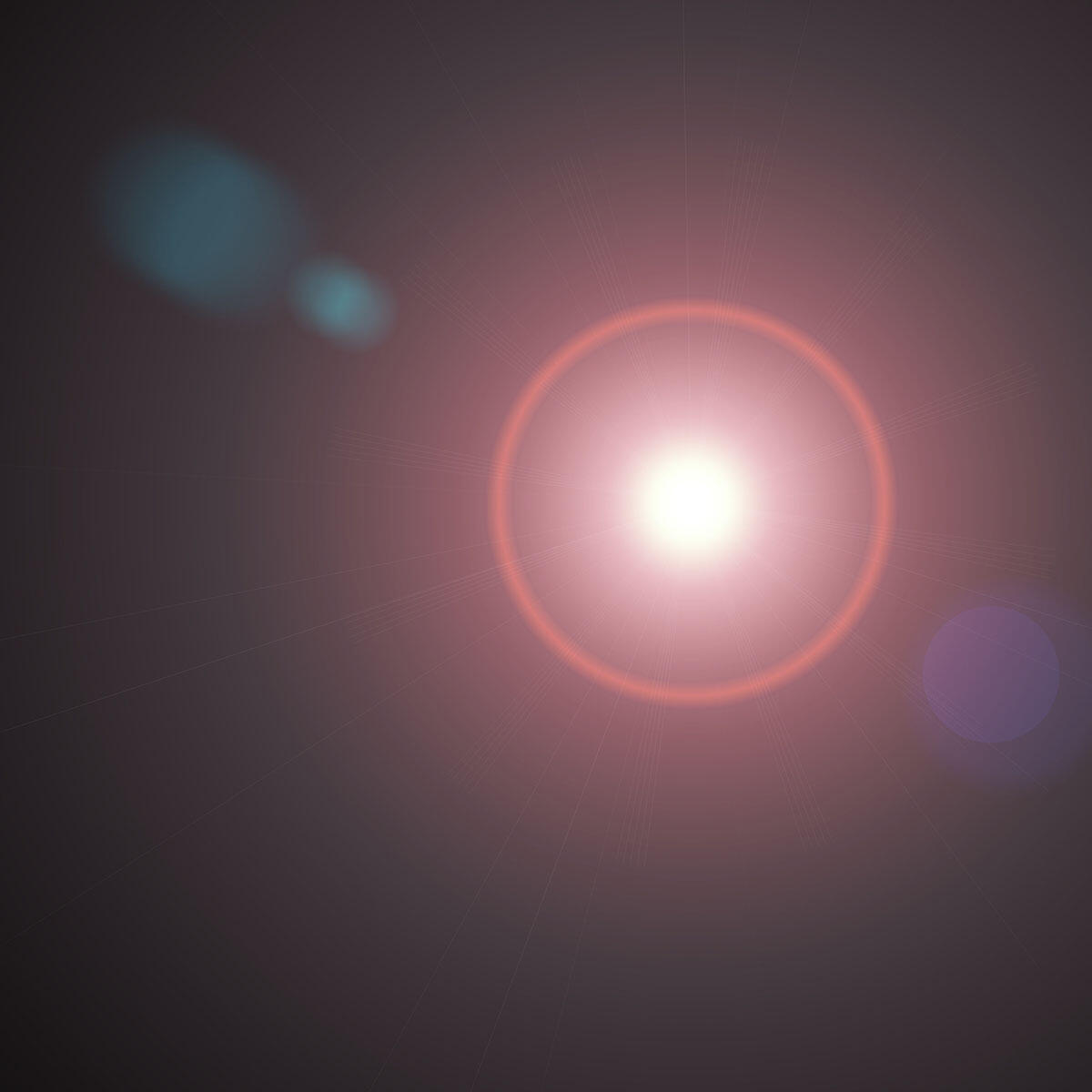
A nanometer is 1/100 million of a meter. No doubt, the world of optics is extremely precise. Every day, our camera components are developed and manufactured at micro levels. One day, a customer asked about a crescent-shaped light reflected in a camera. Chie Fujikawa, who led the project, could not hide her confusion at first.
“These were existing models, products developed before I joined the company …”
Although the product had already been delivered to the client, immediate action was required to investigate any possibility of quality issues. To determine potential causes, she took the product in question back to the factory and conducted a disassembling investigation and a series of inspections. The problem was a phenomenon called Ghosting*, which tends to occur relatively frequently manufacturing camera components. Her field tests confirmed basic product quality was not a problem, but the brightness of the ghost was found to vary from product to product. She determined that the “quality of the product needed to be stabilized”.
*Ghosting occurs when light repeatedly reflects off the surface of the lens and is seen in the image.
Potential Impact:
- Concern about a product already on the market. Fortunately, in this case, the issue was unlikely to lead to a serious accident.
- Conducting selective inspections to stabilize quality. This process strains internal resources during the implementation period, reduces production efficiency, and slows down the design and development of new products.
A manufacturer’s mission encompasses responsibility.
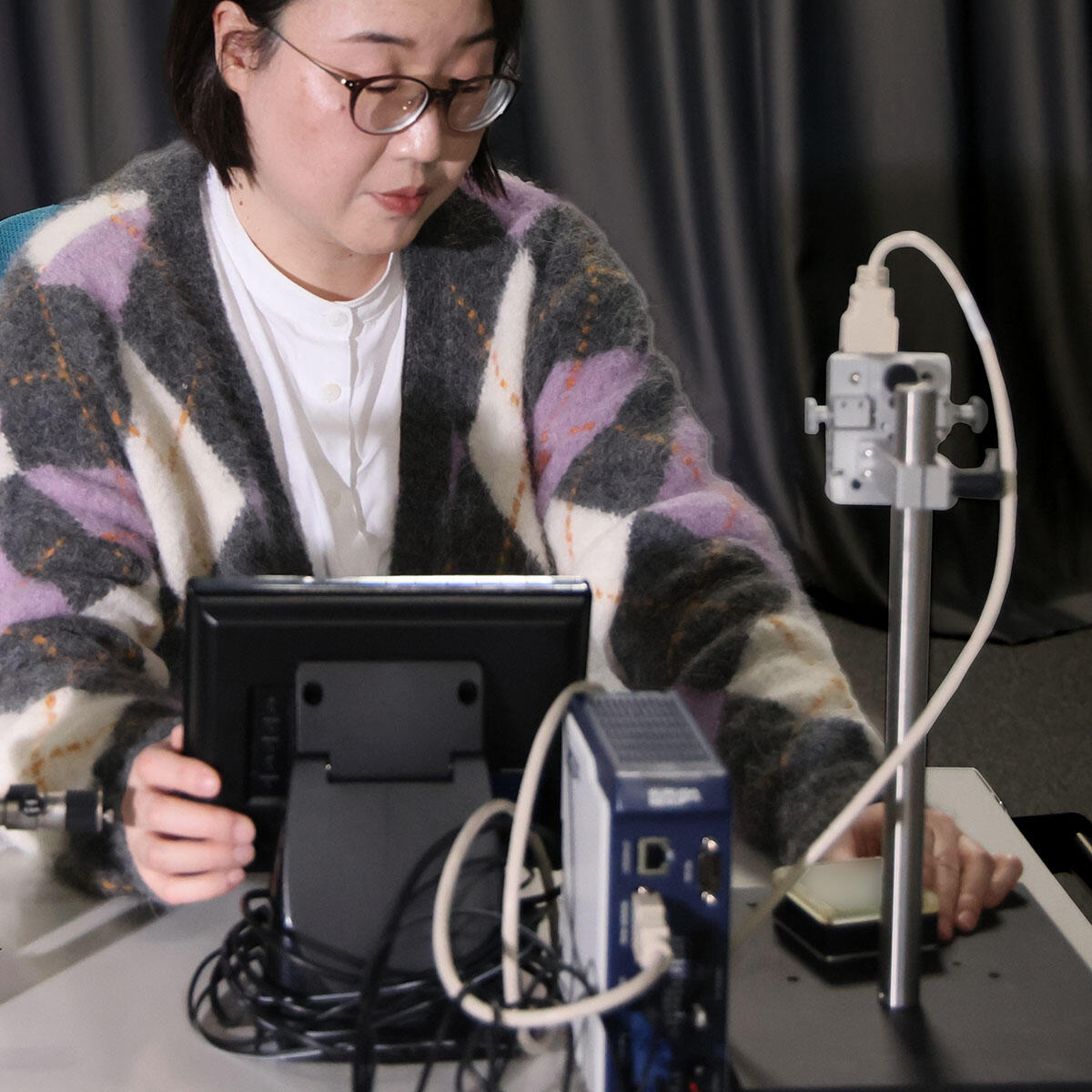
Due to the nature of the product in question, it was considered impossible to completely eliminate ghosting. As a result of her initial internal investigation, Fujikawa also found that the frequency of the bright ghost, which had been reported, was quite low. The supplier agreed that the level of quality was not an issue. However, this was not the end of the challenge. Fujikawa promised further improvements. She asked herself, “When did the discrepancies start and what was the root cause?”
“We did everything we could to find out, conducting a full survey, running simulations using optical analysis tools, and compiling information for future countermeasures,” she explains. During repeated hypothesis testing and trial-and-error sessions, Fujikawa always kept the following philosophy in mind: “As a manufacturer, we must never inconvenience our customers.”
Coordinating her efforts with many sections including production technology, quality assurance, as well as affiliated companies, Fujikawa made steady progress toward quality stabilization. As a result, she succeeded in establishing a more stable and higher-quality production system. From the world of optics to the world of radio waves, Fujikawa is taking on challenges in diverse new fields. While working on camera components, she helped to improve mass production quality and contributed to the design and development of lenses for new products. Currently, in the Research and Development Division, she is focused on the design and development of dielectric lenses for millimeter-wave lens antennas. Her experience in production quality control will likely be a major stepping stone toward the commercialization of dielectric lenses. Her next big challenge.
A message to engineers / What I have learned and earned
Everything has a cause and effect. During mass production, it is not unusual for unexpected defects to occur. Even when we aren’t sure why, we should be able to identify the cause by confronting each potential issue individually through analysis and experimentation. After the cause is identified, countermeasures can be taken to improve quality and increase value. It is not an easy process, but as engineers, we must rise to the challenge. Be confident that your work will eventually become a great source of satisfaction.
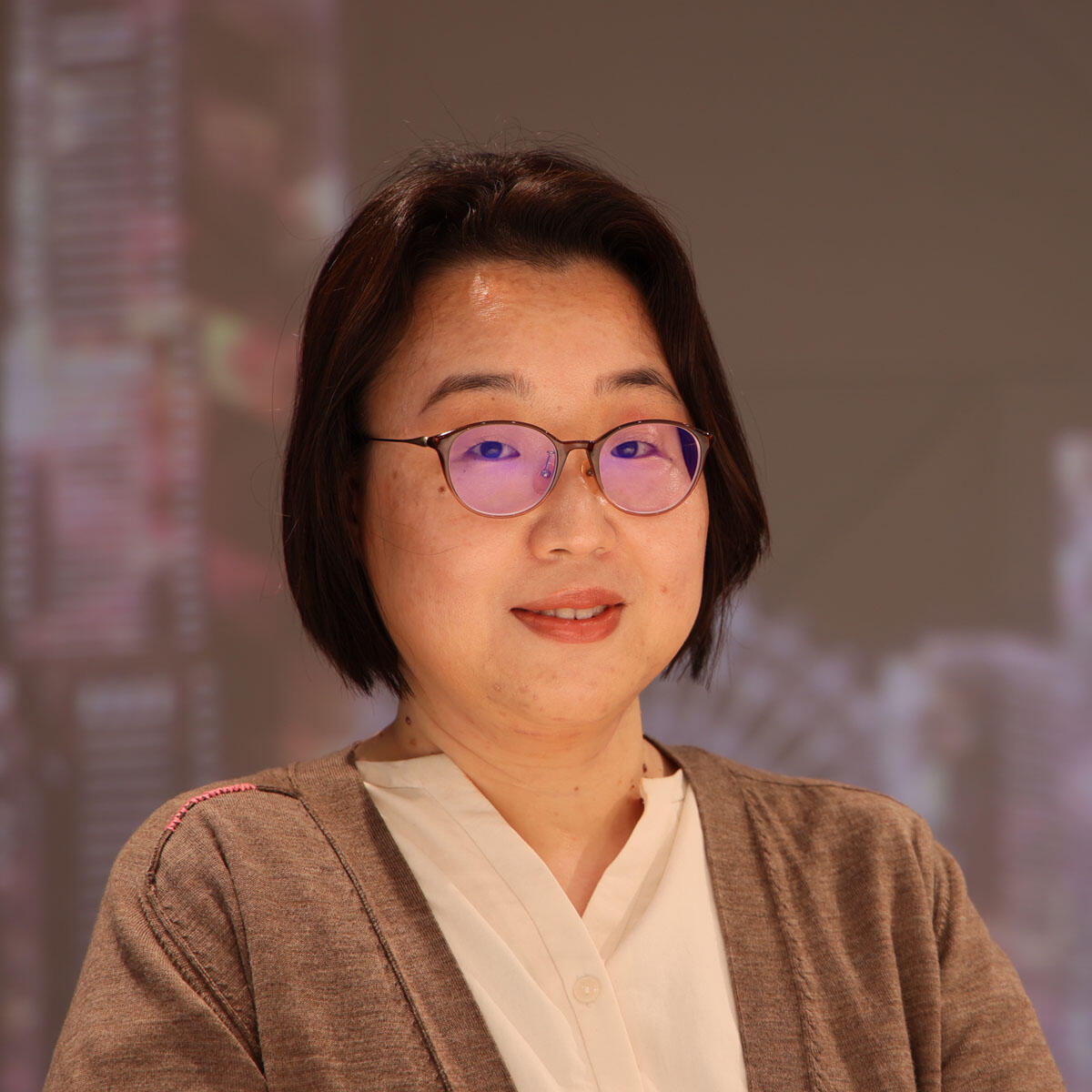
Chie Fujikawa
KYOCERA Corporation, Advanced Technology Research Institute, Corporate R&D Group
Design and development of dielectric lenses for millimeter-wave radar utilizing optics technology.
Articles in the same series
Latest Articles
-
TRENDING TECH
How Lab-Grown Gemstones Are Expanding the Possibilities of Jewelry
-
TRENDING TECH
Forging Partnership for the Sustainable Energy Transition
-
Takumi: The Height of Craft
Episode 3: Choboya - Exploring the similarities between traditional Japanese footwear and printing products
-
TRENDING TECH
The Rise of Realistic Touch - HAPTIVITY® Brings Next-Level Tactile Feedback to Mirrorless Cameras
-
TRENDING TECH
New Air-cooled UV LED Light Source “G7A Series” to enable printing and curing performance
-
KYOCERA TV
Engineer Desk Report: Sven, Business Intelligence Center